What are the Product Standards for Heating Resistors?
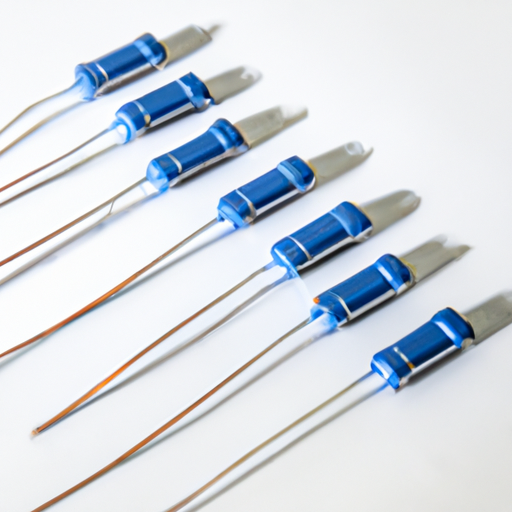
I. Introduction
Heating resistors are essential components in various electrical and electronic applications, converting electrical energy into heat through the principle of resistance. These components are widely used in industries ranging from automotive to consumer electronics, where precise temperature control is crucial. Given their critical role, adhering to product standards is vital for ensuring safety, reliability, and performance. This article will explore the significance of product standards for heating resistors, the key standards that govern their production, and the challenges and future trends in this field.
II. Understanding Heating Resistors
A. Function and Application of Heating Resistors
Heating resistors serve a fundamental purpose: they generate heat when an electric current passes through them. This heat generation is utilized in various applications, including:
1. **Automotive**: In vehicles, heating resistors are used in seat heaters, defrosters, and engine block heaters, providing comfort and enhancing performance.
2. **Manufacturing**: In industrial settings, they are employed in processes such as soldering, plastic molding, and temperature control in ovens.
3. **Consumer Electronics**: Heating resistors are found in appliances like toasters, hair dryers, and electric kettles, where they play a crucial role in heating elements.
B. Basic Principles of Operation
Heating resistors operate on the principle of converting electrical energy into thermal energy. The relationship between resistance and temperature is governed by Ohm's law and the material properties of the resistor. As current flows through the resistor, it encounters resistance, which generates heat. The amount of heat produced is proportional to the square of the current and the resistance value, making it essential to select the appropriate resistor for specific applications.
III. Importance of Product Standards
A. Ensuring Safety and Reliability
Product standards are critical in ensuring that heating resistors operate safely and reliably. Standards provide guidelines for the design, manufacturing, and testing of these components, minimizing the risk of failures that could lead to hazardous situations, such as overheating or electrical fires.
B. Facilitating Compatibility and Interoperability
Adhering to established standards ensures that heating resistors are compatible with other components in a system. This compatibility is crucial for manufacturers who need to integrate various parts into a cohesive unit, ensuring that they function together without issues.
C. Enhancing Performance and Efficiency
Standards often include performance benchmarks that heating resistors must meet. By adhering to these benchmarks, manufacturers can produce components that operate efficiently, reducing energy consumption and improving overall system performance.
D. Regulatory Compliance and Market Access
Compliance with product standards is often a legal requirement for selling electrical components in various markets. Meeting these standards not only ensures safety and reliability but also facilitates access to global markets, allowing manufacturers to expand their reach.
IV. Key Product Standards for Heating Resistors
A. International Standards
1. **IEC (International Electrotechnical Commission) Standards**:
- **IEC 60068**: This standard covers environmental testing, ensuring that heating resistors can withstand various environmental conditions, such as temperature fluctuations, humidity, and vibration.
- **IEC 60115**: This standard specifies the requirements for fixed resistors used in electronic equipment, including heating resistors, focusing on their performance and reliability.
2. **ISO (International Organization for Standardization) Standards**:
- **ISO 9001**: This standard outlines the criteria for a quality management system, ensuring that manufacturers maintain consistent quality in their production processes.
B. National Standards
1. **ANSI (American National Standards Institute) Standards**: ANSI develops standards that ensure the safety and performance of electrical components in the United States, including heating resistors.
2. **UL (Underwriters Laboratories) Standards**: UL provides safety certification for electrical products, ensuring that heating resistors meet stringent safety requirements.
C. Industry-Specific Standards
1. **Automotive Standards**: Standards such as IATF 16949 focus on quality management systems in the automotive industry, ensuring that heating resistors used in vehicles meet specific performance and safety criteria.
2. **Aerospace Standards**: AS9100 is a widely recognized standard in the aerospace industry, emphasizing quality and safety in the production of components, including heating resistors.
V. Testing and Certification Processes
A. Overview of Testing Methods for Heating Resistors
To ensure compliance with product standards, heating resistors undergo various testing methods, including:
1. **Electrical Testing**: This includes measuring resistance, power rating, and ensuring that the resistor operates within specified limits.
2. **Thermal Testing**: Thermal testing evaluates the temperature rise and thermal cycling capabilities of heating resistors, ensuring they can withstand operational conditions without failure.
3. **Environmental Testing**: This testing assesses the performance of heating resistors under different environmental conditions, such as humidity and vibration, to ensure reliability in real-world applications.
B. Certification Bodies and Their Roles
Several certification organizations play a crucial role in the testing and certification of heating resistors:
1. **UL (Underwriters Laboratories)**: UL provides safety certification for electrical products, ensuring they meet established safety standards.
2. **CSA (Canadian Standards Association)**: CSA offers certification for products sold in Canada, focusing on safety and performance.
3. **TUV (Technischer Überwachungsverein)**: TUV is a global certification body that ensures products meet safety and quality standards.
Third-party testing and certification are essential for manufacturers, as they provide an unbiased assessment of product compliance, enhancing credibility and marketability.
VI. Challenges in Meeting Product Standards
A. Technological Advancements and Evolving Standards
As technology advances, product standards must evolve to keep pace with new materials and manufacturing processes. This can create challenges for manufacturers who must continuously adapt their products to meet changing requirements.
B. Cost Implications for Manufacturers
Meeting product standards often involves significant investment in testing, certification, and quality control processes. Smaller manufacturers may find it challenging to bear these costs, potentially limiting their ability to compete in the market.
C. Balancing Performance with Compliance
Manufacturers must strike a balance between optimizing performance and ensuring compliance with standards. This can be particularly challenging when new technologies offer enhanced performance but may not yet be covered by existing standards.
VII. Future Trends in Heating Resistor Standards
A. Innovations in Materials and Technology
The development of new materials and technologies is likely to influence the standards governing heating resistors. Innovations such as advanced ceramics and nanomaterials may lead to the creation of more efficient and durable heating resistors.
B. Increasing Focus on Sustainability and Environmental Impact
As industries become more environmentally conscious, there is a growing emphasis on sustainability in product standards. Future standards may incorporate criteria for the environmental impact of heating resistors, encouraging manufacturers to adopt eco-friendly practices.
C. Anticipated Changes in Regulatory Frameworks
Regulatory frameworks governing electrical components are likely to evolve, with increased scrutiny on safety and performance. Manufacturers must stay informed about these changes to ensure compliance and maintain market access.
VIII. Conclusion
In conclusion, product standards for heating resistors play a vital role in ensuring safety, reliability, and performance across various applications. By adhering to established standards, manufacturers can enhance the quality of their products, facilitate market access, and contribute to the overall safety of electrical systems. As technology continues to advance, it is essential for manufacturers and users to stay informed about evolving standards and best practices in the industry.
IX. References
1. IEC 60068 - Environmental Testing
2. IEC 60115 - Fixed Resistors for Use in Electronic Equipment
3. ISO 9001 - Quality Management Systems
4. ANSI Standards
5. UL Standards
6. IATF 16949 - Automotive Quality Management
7. AS9100 - Aerospace Quality Management
By understanding and adhering to these standards, stakeholders in the heating resistor industry can ensure that they are producing safe, reliable, and efficient products that meet the demands of modern applications.
What are the Product Standards for Heating Resistors?
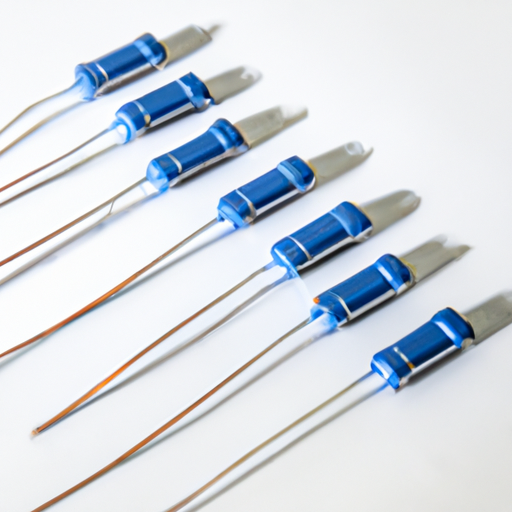
I. Introduction
Heating resistors are essential components in various electrical and electronic applications, converting electrical energy into heat through the principle of resistance. These components are widely used in industries ranging from automotive to consumer electronics, where precise temperature control is crucial. Given their critical role, adhering to product standards is vital for ensuring safety, reliability, and performance. This article will explore the significance of product standards for heating resistors, the key standards that govern their production, and the challenges and future trends in this field.
II. Understanding Heating Resistors
A. Function and Application of Heating Resistors
Heating resistors serve a fundamental purpose: they generate heat when an electric current passes through them. This heat generation is utilized in various applications, including:
1. **Automotive**: In vehicles, heating resistors are used in seat heaters, defrosters, and engine block heaters, providing comfort and enhancing performance.
2. **Manufacturing**: In industrial settings, they are employed in processes such as soldering, plastic molding, and temperature control in ovens.
3. **Consumer Electronics**: Heating resistors are found in appliances like toasters, hair dryers, and electric kettles, where they play a crucial role in heating elements.
B. Basic Principles of Operation
Heating resistors operate on the principle of converting electrical energy into thermal energy. The relationship between resistance and temperature is governed by Ohm's law and the material properties of the resistor. As current flows through the resistor, it encounters resistance, which generates heat. The amount of heat produced is proportional to the square of the current and the resistance value, making it essential to select the appropriate resistor for specific applications.
III. Importance of Product Standards
A. Ensuring Safety and Reliability
Product standards are critical in ensuring that heating resistors operate safely and reliably. Standards provide guidelines for the design, manufacturing, and testing of these components, minimizing the risk of failures that could lead to hazardous situations, such as overheating or electrical fires.
B. Facilitating Compatibility and Interoperability
Adhering to established standards ensures that heating resistors are compatible with other components in a system. This compatibility is crucial for manufacturers who need to integrate various parts into a cohesive unit, ensuring that they function together without issues.
C. Enhancing Performance and Efficiency
Standards often include performance benchmarks that heating resistors must meet. By adhering to these benchmarks, manufacturers can produce components that operate efficiently, reducing energy consumption and improving overall system performance.
D. Regulatory Compliance and Market Access
Compliance with product standards is often a legal requirement for selling electrical components in various markets. Meeting these standards not only ensures safety and reliability but also facilitates access to global markets, allowing manufacturers to expand their reach.
IV. Key Product Standards for Heating Resistors
A. International Standards
1. **IEC (International Electrotechnical Commission) Standards**:
- **IEC 60068**: This standard covers environmental testing, ensuring that heating resistors can withstand various environmental conditions, such as temperature fluctuations, humidity, and vibration.
- **IEC 60115**: This standard specifies the requirements for fixed resistors used in electronic equipment, including heating resistors, focusing on their performance and reliability.
2. **ISO (International Organization for Standardization) Standards**:
- **ISO 9001**: This standard outlines the criteria for a quality management system, ensuring that manufacturers maintain consistent quality in their production processes.
B. National Standards
1. **ANSI (American National Standards Institute) Standards**: ANSI develops standards that ensure the safety and performance of electrical components in the United States, including heating resistors.
2. **UL (Underwriters Laboratories) Standards**: UL provides safety certification for electrical products, ensuring that heating resistors meet stringent safety requirements.
C. Industry-Specific Standards
1. **Automotive Standards**: Standards such as IATF 16949 focus on quality management systems in the automotive industry, ensuring that heating resistors used in vehicles meet specific performance and safety criteria.
2. **Aerospace Standards**: AS9100 is a widely recognized standard in the aerospace industry, emphasizing quality and safety in the production of components, including heating resistors.
V. Testing and Certification Processes
A. Overview of Testing Methods for Heating Resistors
To ensure compliance with product standards, heating resistors undergo various testing methods, including:
1. **Electrical Testing**: This includes measuring resistance, power rating, and ensuring that the resistor operates within specified limits.
2. **Thermal Testing**: Thermal testing evaluates the temperature rise and thermal cycling capabilities of heating resistors, ensuring they can withstand operational conditions without failure.
3. **Environmental Testing**: This testing assesses the performance of heating resistors under different environmental conditions, such as humidity and vibration, to ensure reliability in real-world applications.
B. Certification Bodies and Their Roles
Several certification organizations play a crucial role in the testing and certification of heating resistors:
1. **UL (Underwriters Laboratories)**: UL provides safety certification for electrical products, ensuring they meet established safety standards.
2. **CSA (Canadian Standards Association)**: CSA offers certification for products sold in Canada, focusing on safety and performance.
3. **TUV (Technischer Überwachungsverein)**: TUV is a global certification body that ensures products meet safety and quality standards.
Third-party testing and certification are essential for manufacturers, as they provide an unbiased assessment of product compliance, enhancing credibility and marketability.
VI. Challenges in Meeting Product Standards
A. Technological Advancements and Evolving Standards
As technology advances, product standards must evolve to keep pace with new materials and manufacturing processes. This can create challenges for manufacturers who must continuously adapt their products to meet changing requirements.
B. Cost Implications for Manufacturers
Meeting product standards often involves significant investment in testing, certification, and quality control processes. Smaller manufacturers may find it challenging to bear these costs, potentially limiting their ability to compete in the market.
C. Balancing Performance with Compliance
Manufacturers must strike a balance between optimizing performance and ensuring compliance with standards. This can be particularly challenging when new technologies offer enhanced performance but may not yet be covered by existing standards.
VII. Future Trends in Heating Resistor Standards
A. Innovations in Materials and Technology
The development of new materials and technologies is likely to influence the standards governing heating resistors. Innovations such as advanced ceramics and nanomaterials may lead to the creation of more efficient and durable heating resistors.
B. Increasing Focus on Sustainability and Environmental Impact
As industries become more environmentally conscious, there is a growing emphasis on sustainability in product standards. Future standards may incorporate criteria for the environmental impact of heating resistors, encouraging manufacturers to adopt eco-friendly practices.
C. Anticipated Changes in Regulatory Frameworks
Regulatory frameworks governing electrical components are likely to evolve, with increased scrutiny on safety and performance. Manufacturers must stay informed about these changes to ensure compliance and maintain market access.
VIII. Conclusion
In conclusion, product standards for heating resistors play a vital role in ensuring safety, reliability, and performance across various applications. By adhering to established standards, manufacturers can enhance the quality of their products, facilitate market access, and contribute to the overall safety of electrical systems. As technology continues to advance, it is essential for manufacturers and users to stay informed about evolving standards and best practices in the industry.
IX. References
1. IEC 60068 - Environmental Testing
2. IEC 60115 - Fixed Resistors for Use in Electronic Equipment
3. ISO 9001 - Quality Management Systems
4. ANSI Standards
5. UL Standards
6. IATF 16949 - Automotive Quality Management
7. AS9100 - Aerospace Quality Management
By understanding and adhering to these standards, stakeholders in the heating resistor industry can ensure that they are producing safe, reliable, and efficient products that meet the demands of modern applications.