What are the Product Features of a Resistor Factory?
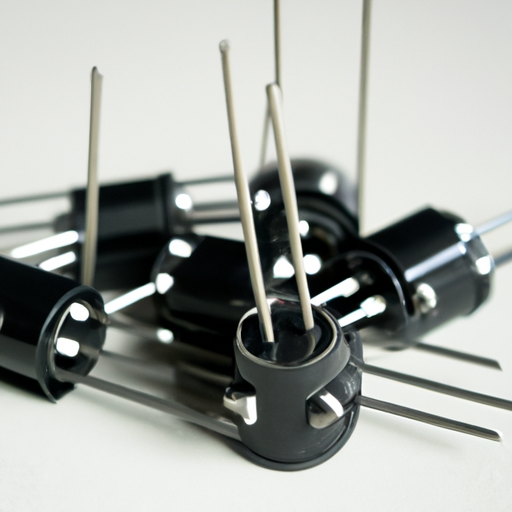
I. Introduction
A. Definition of Resistors
Resistors are passive electronic components that limit the flow of electric current in a circuit. They are essential for controlling voltage and current levels, ensuring that electronic devices operate safely and effectively. By providing a specific resistance value, resistors help to manage the electrical characteristics of circuits, making them crucial in a wide range of applications.
B. Importance of Resistors in Electronic Circuits
In electronic circuits, resistors play a vital role in protecting sensitive components from excessive current, dividing voltages, and setting bias points for transistors. They are found in virtually every electronic device, from simple household appliances to complex industrial machinery. Without resistors, circuits would be prone to failure, leading to malfunctions and potential hazards.
C. Overview of Resistor Manufacturing
The manufacturing of resistors involves a series of intricate processes that transform raw materials into reliable electronic components. Resistor factories utilize advanced technologies and quality control measures to produce a variety of resistor types, each tailored to meet specific electrical and physical requirements. This blog post will explore the product features of a resistor factory, including the types of resistors produced, manufacturing processes, and the latest technological innovations.
II. Types of Resistors
A. Fixed Resistors
Fixed resistors are the most common type, providing a constant resistance value. They are categorized into several subtypes:
1. **Carbon Composition Resistors**: Made from a mixture of carbon and a binding material, these resistors are known for their high energy absorption and ability to withstand high temperatures. However, they have a wider tolerance range and are less stable than other types.
2. **Metal Film Resistors**: These resistors are constructed using a thin film of metal deposited on a ceramic substrate. They offer better stability, lower noise, and tighter tolerance levels compared to carbon composition resistors, making them ideal for precision applications.
3. **Wirewound Resistors**: Made by winding a metal wire around a ceramic or fiberglass core, wirewound resistors can handle high power levels and are often used in applications requiring high precision and stability.
B. Variable Resistors
Variable resistors allow for adjustable resistance values, making them versatile components in electronic circuits.
1. **Potentiometers**: These are commonly used for volume control in audio equipment and as adjustable voltage dividers in various applications.
2. **Rheostats**: Similar to potentiometers, rheostats are used to control current flow in a circuit. They are often employed in applications requiring high power handling.
C. Specialty Resistors
Specialty resistors are designed for specific applications and include:
1. **Thermistors**: Temperature-sensitive resistors that change resistance with temperature variations, thermistors are widely used in temperature sensing and control applications.
2. **Photoresistors**: Also known as light-dependent resistors (LDRs), these components change resistance based on light exposure, making them useful in light-sensing applications.
III. Manufacturing Processes
A. Material Selection
The selection of materials is critical in resistor manufacturing. Key materials include:
1. **Conductive Materials**: Common conductive materials include carbon, metal films, and metal wires, each chosen based on the desired electrical characteristics.
2. **Insulating Materials**: Insulators, such as ceramics and plastics, are used to encase resistors, ensuring safety and reliability in electrical applications.
B. Production Techniques
Resistor factories employ various production techniques, including:
1. **Thin Film Technology**: This method involves depositing a thin layer of resistive material onto a substrate, allowing for precise control over resistance values and improved performance.
2. **Thick Film Technology**: In this technique, a thicker layer of resistive paste is printed onto a substrate, providing a cost-effective solution for mass production.
3. **Wirewound Techniques**: Wirewound resistors are manufactured by winding a metal wire around a core, offering high power ratings and stability.
C. Quality Control Measures
Quality control is paramount in resistor manufacturing. Factories implement rigorous testing procedures to ensure that products meet industry standards, such as ISO and RoHS compliance. This includes:
1. **Testing Procedures**: Resistors undergo various tests, including resistance measurement, temperature coefficient testing, and power rating assessments.
2. **Compliance with Standards**: Adhering to international standards ensures that resistors are safe, reliable, and suitable for use in electronic devices.
IV. Product Features
A. Electrical Characteristics
The electrical characteristics of resistors are crucial for their performance:
1. **Resistance Value Range**: Resistors are available in a wide range of resistance values, from ohms to megaohms, allowing for diverse applications.
2. **Tolerance Levels**: Tolerance indicates the precision of a resistor's resistance value. Common tolerance levels include ±1%, ±5%, and ±10%, with tighter tolerances available for specialized applications.
3. **Power Rating**: The power rating indicates the maximum power a resistor can dissipate without overheating. Resistors are available in various power ratings, from milliwatts to several watts.
B. Physical Characteristics
Physical characteristics also play a significant role in resistor selection:
1. **Size and Form Factor**: Resistors come in various sizes and shapes, including axial, radial, and surface-mount configurations, allowing for flexibility in circuit design.
2. **Packaging Options**: Resistors can be packaged in bulk or as individual components, catering to different manufacturing needs.
C. Environmental Considerations
Environmental factors are increasingly important in resistor manufacturing:
1. **Temperature Coefficient**: This measures how much a resistor's resistance changes with temperature. Low-temperature coefficient resistors are preferred in precision applications.
2. **Moisture Resistance**: Resistors must be designed to withstand moisture and humidity, especially in outdoor or high-humidity environments.
3. **Lead-Free Options**: With growing environmental concerns, many manufacturers offer lead-free resistors to comply with regulations and promote sustainability.
V. Customization and Special Orders
A. Custom Resistance Values
Resistor factories often provide customization options, allowing customers to specify unique resistance values that meet their specific needs.
B. Unique Packaging Solutions
Manufacturers can also offer tailored packaging solutions, ensuring that resistors are delivered in a manner that suits the customer's production processes.
C. Specialized Applications
Resistors can be designed for specialized applications, such as automotive and aerospace, where performance and reliability are critical.
VI. Technological Innovations
A. Smart Resistors
The advent of smart technology has led to the development of smart resistors, which can provide real-time data on their performance and health, enhancing circuit reliability.
B. Integration with IoT Devices
As the Internet of Things (IoT) continues to grow, resistors are being integrated into smart devices, enabling better control and monitoring of electronic systems.
C. Advances in Material Science
Ongoing research in material science is leading to the development of new resistor materials that offer improved performance, stability, and environmental resistance.
VII. Market Trends and Demand
A. Growing Electronics Market
The demand for resistors is closely tied to the growth of the electronics market, driven by advancements in technology and increasing consumer electronics usage.
B. Impact of Renewable Energy Technologies
The rise of renewable energy technologies, such as solar and wind power, has created new opportunities for resistor manufacturers, as these systems require reliable components for efficient operation.
C. Trends in Consumer Electronics
Consumer electronics continue to evolve, with trends such as miniaturization and increased functionality driving the demand for high-quality resistors.
VIII. Conclusion
A. Summary of Key Features
Resistor factories play a crucial role in the electronics industry, producing a wide range of resistors with various electrical and physical characteristics. From fixed and variable resistors to specialty options, the diversity of products ensures that there is a suitable resistor for every application.
B. Future Outlook for Resistor Manufacturing
As technology continues to advance, the future of resistor manufacturing looks promising. Innovations in materials, production techniques, and smart technology will drive the development of more efficient and reliable resistors.
C. Importance of Resistors in Modern Technology
In conclusion, resistors are fundamental components in modern technology, enabling the safe and efficient operation of electronic devices. Their continued evolution will be essential in meeting the demands of an increasingly connected and technologically advanced world.
IX. References
A. Academic Journals
- Journal of Electronic Materials
- IEEE Transactions on Components, Packaging and Manufacturing Technology
B. Industry Reports
- Market Research Reports on Resistor Manufacturing
- Global Electronics Market Analysis
C. Manufacturer Specifications
- Datasheets from leading resistor manufacturers
- Compliance documentation for industry standards
This comprehensive overview of the product features of a resistor factory highlights the importance of resistors in electronic circuits and the intricate processes involved in their manufacturing. As technology evolves, so too will the capabilities and applications of resistors, ensuring their relevance in the future of electronics.
What are the Product Features of a Resistor Factory?
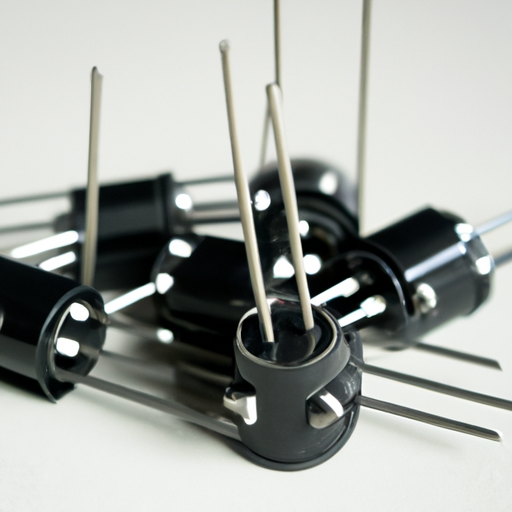
I. Introduction
A. Definition of Resistors
Resistors are passive electronic components that limit the flow of electric current in a circuit. They are essential for controlling voltage and current levels, ensuring that electronic devices operate safely and effectively. By providing a specific resistance value, resistors help to manage the electrical characteristics of circuits, making them crucial in a wide range of applications.
B. Importance of Resistors in Electronic Circuits
In electronic circuits, resistors play a vital role in protecting sensitive components from excessive current, dividing voltages, and setting bias points for transistors. They are found in virtually every electronic device, from simple household appliances to complex industrial machinery. Without resistors, circuits would be prone to failure, leading to malfunctions and potential hazards.
C. Overview of Resistor Manufacturing
The manufacturing of resistors involves a series of intricate processes that transform raw materials into reliable electronic components. Resistor factories utilize advanced technologies and quality control measures to produce a variety of resistor types, each tailored to meet specific electrical and physical requirements. This blog post will explore the product features of a resistor factory, including the types of resistors produced, manufacturing processes, and the latest technological innovations.
II. Types of Resistors
A. Fixed Resistors
Fixed resistors are the most common type, providing a constant resistance value. They are categorized into several subtypes:
1. **Carbon Composition Resistors**: Made from a mixture of carbon and a binding material, these resistors are known for their high energy absorption and ability to withstand high temperatures. However, they have a wider tolerance range and are less stable than other types.
2. **Metal Film Resistors**: These resistors are constructed using a thin film of metal deposited on a ceramic substrate. They offer better stability, lower noise, and tighter tolerance levels compared to carbon composition resistors, making them ideal for precision applications.
3. **Wirewound Resistors**: Made by winding a metal wire around a ceramic or fiberglass core, wirewound resistors can handle high power levels and are often used in applications requiring high precision and stability.
B. Variable Resistors
Variable resistors allow for adjustable resistance values, making them versatile components in electronic circuits.
1. **Potentiometers**: These are commonly used for volume control in audio equipment and as adjustable voltage dividers in various applications.
2. **Rheostats**: Similar to potentiometers, rheostats are used to control current flow in a circuit. They are often employed in applications requiring high power handling.
C. Specialty Resistors
Specialty resistors are designed for specific applications and include:
1. **Thermistors**: Temperature-sensitive resistors that change resistance with temperature variations, thermistors are widely used in temperature sensing and control applications.
2. **Photoresistors**: Also known as light-dependent resistors (LDRs), these components change resistance based on light exposure, making them useful in light-sensing applications.
III. Manufacturing Processes
A. Material Selection
The selection of materials is critical in resistor manufacturing. Key materials include:
1. **Conductive Materials**: Common conductive materials include carbon, metal films, and metal wires, each chosen based on the desired electrical characteristics.
2. **Insulating Materials**: Insulators, such as ceramics and plastics, are used to encase resistors, ensuring safety and reliability in electrical applications.
B. Production Techniques
Resistor factories employ various production techniques, including:
1. **Thin Film Technology**: This method involves depositing a thin layer of resistive material onto a substrate, allowing for precise control over resistance values and improved performance.
2. **Thick Film Technology**: In this technique, a thicker layer of resistive paste is printed onto a substrate, providing a cost-effective solution for mass production.
3. **Wirewound Techniques**: Wirewound resistors are manufactured by winding a metal wire around a core, offering high power ratings and stability.
C. Quality Control Measures
Quality control is paramount in resistor manufacturing. Factories implement rigorous testing procedures to ensure that products meet industry standards, such as ISO and RoHS compliance. This includes:
1. **Testing Procedures**: Resistors undergo various tests, including resistance measurement, temperature coefficient testing, and power rating assessments.
2. **Compliance with Standards**: Adhering to international standards ensures that resistors are safe, reliable, and suitable for use in electronic devices.
IV. Product Features
A. Electrical Characteristics
The electrical characteristics of resistors are crucial for their performance:
1. **Resistance Value Range**: Resistors are available in a wide range of resistance values, from ohms to megaohms, allowing for diverse applications.
2. **Tolerance Levels**: Tolerance indicates the precision of a resistor's resistance value. Common tolerance levels include ±1%, ±5%, and ±10%, with tighter tolerances available for specialized applications.
3. **Power Rating**: The power rating indicates the maximum power a resistor can dissipate without overheating. Resistors are available in various power ratings, from milliwatts to several watts.
B. Physical Characteristics
Physical characteristics also play a significant role in resistor selection:
1. **Size and Form Factor**: Resistors come in various sizes and shapes, including axial, radial, and surface-mount configurations, allowing for flexibility in circuit design.
2. **Packaging Options**: Resistors can be packaged in bulk or as individual components, catering to different manufacturing needs.
C. Environmental Considerations
Environmental factors are increasingly important in resistor manufacturing:
1. **Temperature Coefficient**: This measures how much a resistor's resistance changes with temperature. Low-temperature coefficient resistors are preferred in precision applications.
2. **Moisture Resistance**: Resistors must be designed to withstand moisture and humidity, especially in outdoor or high-humidity environments.
3. **Lead-Free Options**: With growing environmental concerns, many manufacturers offer lead-free resistors to comply with regulations and promote sustainability.
V. Customization and Special Orders
A. Custom Resistance Values
Resistor factories often provide customization options, allowing customers to specify unique resistance values that meet their specific needs.
B. Unique Packaging Solutions
Manufacturers can also offer tailored packaging solutions, ensuring that resistors are delivered in a manner that suits the customer's production processes.
C. Specialized Applications
Resistors can be designed for specialized applications, such as automotive and aerospace, where performance and reliability are critical.
VI. Technological Innovations
A. Smart Resistors
The advent of smart technology has led to the development of smart resistors, which can provide real-time data on their performance and health, enhancing circuit reliability.
B. Integration with IoT Devices
As the Internet of Things (IoT) continues to grow, resistors are being integrated into smart devices, enabling better control and monitoring of electronic systems.
C. Advances in Material Science
Ongoing research in material science is leading to the development of new resistor materials that offer improved performance, stability, and environmental resistance.
VII. Market Trends and Demand
A. Growing Electronics Market
The demand for resistors is closely tied to the growth of the electronics market, driven by advancements in technology and increasing consumer electronics usage.
B. Impact of Renewable Energy Technologies
The rise of renewable energy technologies, such as solar and wind power, has created new opportunities for resistor manufacturers, as these systems require reliable components for efficient operation.
C. Trends in Consumer Electronics
Consumer electronics continue to evolve, with trends such as miniaturization and increased functionality driving the demand for high-quality resistors.
VIII. Conclusion
A. Summary of Key Features
Resistor factories play a crucial role in the electronics industry, producing a wide range of resistors with various electrical and physical characteristics. From fixed and variable resistors to specialty options, the diversity of products ensures that there is a suitable resistor for every application.
B. Future Outlook for Resistor Manufacturing
As technology continues to advance, the future of resistor manufacturing looks promising. Innovations in materials, production techniques, and smart technology will drive the development of more efficient and reliable resistors.
C. Importance of Resistors in Modern Technology
In conclusion, resistors are fundamental components in modern technology, enabling the safe and efficient operation of electronic devices. Their continued evolution will be essential in meeting the demands of an increasingly connected and technologically advanced world.
IX. References
A. Academic Journals
- Journal of Electronic Materials
- IEEE Transactions on Components, Packaging and Manufacturing Technology
B. Industry Reports
- Market Research Reports on Resistor Manufacturing
- Global Electronics Market Analysis
C. Manufacturer Specifications
- Datasheets from leading resistor manufacturers
- Compliance documentation for industry standards
This comprehensive overview of the product features of a resistor factory highlights the importance of resistors in electronic circuits and the intricate processes involved in their manufacturing. As technology evolves, so too will the capabilities and applications of resistors, ensuring their relevance in the future of electronics.