Common Production Processes for Resistor Standards
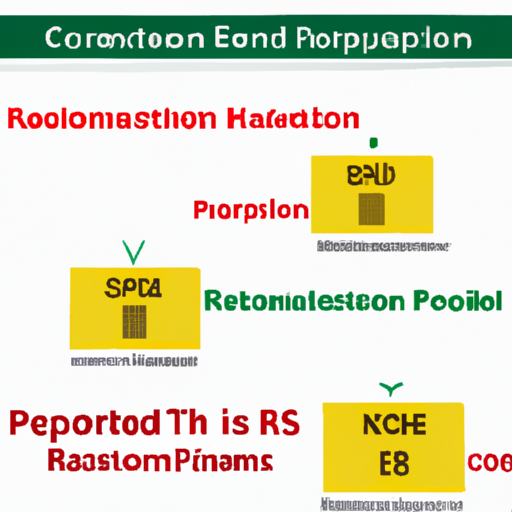
I. Introduction
Resistor standards are essential components in the world of electronics, serving as benchmarks for resistance values in various applications. These standards ensure that electronic devices function correctly and reliably, making them crucial for both consumer and industrial electronics. The production of resistor standards involves a series of intricate processes that transform raw materials into precise and reliable components. This blog post will explore the common production processes for resistor standards, delving into the types of resistors, raw materials, manufacturing techniques, challenges, and innovations in the field.
II. Types of Resistor Standards
Resistors can be broadly categorized into fixed and variable types, each serving different purposes in electronic circuits.
A. Fixed Resistors
1. **Carbon Composition Resistors**: These resistors are made from a mixture of carbon and a binding material. They are known for their high energy absorption and are often used in applications where high pulse loads are expected.
2. **Metal Film Resistors**: Constructed from a thin film of metal, these resistors offer high precision and stability. They are widely used in applications requiring accurate resistance values.
3. **Wirewound Resistors**: Made by winding a metal wire around a ceramic or insulating core, wirewound resistors are known for their high power ratings and are often used in high-current applications.
B. Variable Resistors
1. **Potentiometers**: These resistors allow for adjustable resistance and are commonly used in volume controls and other applications where variable resistance is needed.
2. **Rheostats**: Similar to potentiometers, rheostats are used to control current flow in a circuit, but they typically handle higher power levels.
C. Specialty Resistors
1. **Precision Resistors**: Designed for applications requiring high accuracy, precision resistors are manufactured with tight tolerances and are often used in measurement and calibration equipment.
2. **High-Temperature Resistors**: These resistors are engineered to operate in extreme temperatures, making them suitable for applications in harsh environments, such as automotive and aerospace industries.
III. Raw Materials Used in Resistor Production
The production of resistors relies on a variety of raw materials, each contributing to the performance and reliability of the final product.
A. Conductive Materials
1. **Carbon**: Used primarily in carbon composition resistors, carbon provides a stable resistance value and is cost-effective.
2. **Metal Oxides**: Commonly used in metal film resistors, metal oxides offer excellent temperature stability and are resistant to environmental factors.
3. **Metal Alloys**: Wirewound resistors often utilize metal alloys, which provide high conductivity and durability.
B. Insulating Materials
1. **Ceramics**: Used as a substrate in wirewound and thick film resistors, ceramics provide excellent thermal stability and electrical insulation.
2. **Epoxy Resins**: These materials are used for encapsulating resistors, providing protection against moisture and mechanical stress.
3. **Plastics**: Often used in variable resistors, plastics offer flexibility and durability in various applications.
IV. Common Production Processes
The production of resistor standards involves several key processes, each critical to ensuring the quality and reliability of the final product.
A. Design and Prototyping
1. **Electrical Specifications**: The first step in resistor production is defining the electrical specifications, including resistance value, tolerance, and temperature coefficient.
2. **Mechanical Design**: Engineers create mechanical designs that consider factors such as size, shape, and mounting options to ensure compatibility with electronic devices.
B. Material Preparation
1. **Sourcing Raw Materials**: Manufacturers source high-quality raw materials from reliable suppliers to ensure consistent performance.
2. **Material Processing Techniques**: Raw materials undergo various processing techniques, such as grinding, mixing, and shaping, to prepare them for manufacturing.
C. Manufacturing Techniques
1. **Thin Film Technology**:
- **Deposition Methods**: Thin film resistors are produced by depositing a thin layer of resistive material onto a substrate using techniques like sputtering or chemical vapor deposition.
- **Patterning Techniques**: After deposition, the resistive layer is patterned using photolithography to create the desired resistance value.
2. **Thick Film Technology**:
- **Screen Printing**: In thick film resistors, a paste made from conductive materials is screen-printed onto a ceramic substrate.
- **Firing Process**: The printed resistive layer is then fired at high temperatures to sinter the materials and achieve the desired electrical properties.
3. **Wirewound Techniques**:
- **Winding Process**: A metal wire is wound around a ceramic or insulating core to create the resistor. The number of turns and wire gauge determine the resistance value.
- **Encapsulation**: The wound resistor is encapsulated in a protective material to enhance durability and reliability.
D. Quality Control and Testing
1. **Electrical Testing**: Each resistor undergoes electrical testing to verify its resistance value, tolerance, and temperature coefficient.
2. **Environmental Testing**: Resistors are subjected to environmental tests, including humidity, temperature cycling, and vibration, to ensure they can withstand real-world conditions.
3. **Calibration Procedures**: Precision resistors are calibrated against known standards to ensure their accuracy and reliability.
V. Challenges in Resistor Production
Despite advancements in technology, resistor production faces several challenges:
A. Tolerance and Precision
Achieving tight tolerances and high precision in resistor manufacturing is critical, especially for applications in measurement and calibration. Variations in raw materials and manufacturing processes can impact the final product's performance.
B. Temperature Coefficients
Resistors must maintain stable resistance values across varying temperatures. Manufacturers must carefully select materials and design processes to minimize temperature coefficients.
C. Material Availability and Cost
The availability and cost of raw materials can fluctuate, impacting production costs and timelines. Manufacturers must navigate these challenges to maintain competitive pricing and quality.
VI. Innovations in Resistor Production
The resistor production industry is continually evolving, with innovations aimed at improving efficiency, quality, and sustainability.
A. Advances in Materials Science
Research into new materials and composites is leading to the development of resistors with enhanced performance characteristics, such as improved temperature stability and lower noise levels.
B. Automation and Industry 4.0
The integration of automation and smart manufacturing technologies is streamlining production processes, reducing labor costs, and increasing production efficiency.
C. Sustainable Practices in Production
Manufacturers are increasingly adopting sustainable practices, such as recycling materials and reducing waste, to minimize their environmental impact.
VII. Conclusion
In summary, the production of resistor standards is a complex process that involves various types of resistors, raw materials, and manufacturing techniques. The challenges faced in achieving precision and reliability are met with ongoing innovations in materials science and production methods. As technology continues to advance, the role of resistor standards in electronics will remain vital, ensuring the performance and reliability of electronic devices across industries.
VIII. References
A comprehensive list of academic journals, industry reports, and publications from standards organizations can provide further insights into the production processes and innovations in resistor standards. These resources are invaluable for anyone looking to deepen their understanding of this critical component in electronics.
Common Production Processes for Resistor Standards
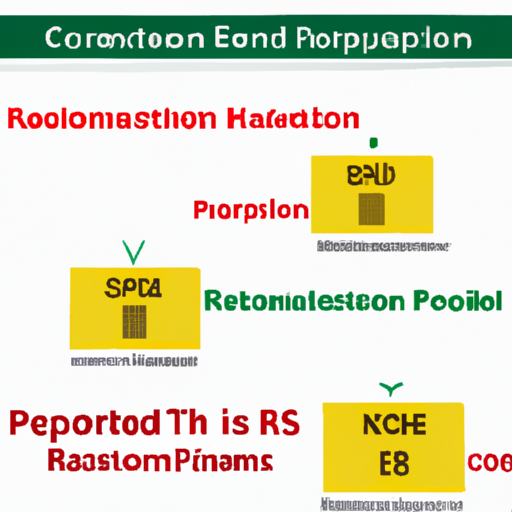
I. Introduction
Resistor standards are essential components in the world of electronics, serving as benchmarks for resistance values in various applications. These standards ensure that electronic devices function correctly and reliably, making them crucial for both consumer and industrial electronics. The production of resistor standards involves a series of intricate processes that transform raw materials into precise and reliable components. This blog post will explore the common production processes for resistor standards, delving into the types of resistors, raw materials, manufacturing techniques, challenges, and innovations in the field.
II. Types of Resistor Standards
Resistors can be broadly categorized into fixed and variable types, each serving different purposes in electronic circuits.
A. Fixed Resistors
1. **Carbon Composition Resistors**: These resistors are made from a mixture of carbon and a binding material. They are known for their high energy absorption and are often used in applications where high pulse loads are expected.
2. **Metal Film Resistors**: Constructed from a thin film of metal, these resistors offer high precision and stability. They are widely used in applications requiring accurate resistance values.
3. **Wirewound Resistors**: Made by winding a metal wire around a ceramic or insulating core, wirewound resistors are known for their high power ratings and are often used in high-current applications.
B. Variable Resistors
1. **Potentiometers**: These resistors allow for adjustable resistance and are commonly used in volume controls and other applications where variable resistance is needed.
2. **Rheostats**: Similar to potentiometers, rheostats are used to control current flow in a circuit, but they typically handle higher power levels.
C. Specialty Resistors
1. **Precision Resistors**: Designed for applications requiring high accuracy, precision resistors are manufactured with tight tolerances and are often used in measurement and calibration equipment.
2. **High-Temperature Resistors**: These resistors are engineered to operate in extreme temperatures, making them suitable for applications in harsh environments, such as automotive and aerospace industries.
III. Raw Materials Used in Resistor Production
The production of resistors relies on a variety of raw materials, each contributing to the performance and reliability of the final product.
A. Conductive Materials
1. **Carbon**: Used primarily in carbon composition resistors, carbon provides a stable resistance value and is cost-effective.
2. **Metal Oxides**: Commonly used in metal film resistors, metal oxides offer excellent temperature stability and are resistant to environmental factors.
3. **Metal Alloys**: Wirewound resistors often utilize metal alloys, which provide high conductivity and durability.
B. Insulating Materials
1. **Ceramics**: Used as a substrate in wirewound and thick film resistors, ceramics provide excellent thermal stability and electrical insulation.
2. **Epoxy Resins**: These materials are used for encapsulating resistors, providing protection against moisture and mechanical stress.
3. **Plastics**: Often used in variable resistors, plastics offer flexibility and durability in various applications.
IV. Common Production Processes
The production of resistor standards involves several key processes, each critical to ensuring the quality and reliability of the final product.
A. Design and Prototyping
1. **Electrical Specifications**: The first step in resistor production is defining the electrical specifications, including resistance value, tolerance, and temperature coefficient.
2. **Mechanical Design**: Engineers create mechanical designs that consider factors such as size, shape, and mounting options to ensure compatibility with electronic devices.
B. Material Preparation
1. **Sourcing Raw Materials**: Manufacturers source high-quality raw materials from reliable suppliers to ensure consistent performance.
2. **Material Processing Techniques**: Raw materials undergo various processing techniques, such as grinding, mixing, and shaping, to prepare them for manufacturing.
C. Manufacturing Techniques
1. **Thin Film Technology**:
- **Deposition Methods**: Thin film resistors are produced by depositing a thin layer of resistive material onto a substrate using techniques like sputtering or chemical vapor deposition.
- **Patterning Techniques**: After deposition, the resistive layer is patterned using photolithography to create the desired resistance value.
2. **Thick Film Technology**:
- **Screen Printing**: In thick film resistors, a paste made from conductive materials is screen-printed onto a ceramic substrate.
- **Firing Process**: The printed resistive layer is then fired at high temperatures to sinter the materials and achieve the desired electrical properties.
3. **Wirewound Techniques**:
- **Winding Process**: A metal wire is wound around a ceramic or insulating core to create the resistor. The number of turns and wire gauge determine the resistance value.
- **Encapsulation**: The wound resistor is encapsulated in a protective material to enhance durability and reliability.
D. Quality Control and Testing
1. **Electrical Testing**: Each resistor undergoes electrical testing to verify its resistance value, tolerance, and temperature coefficient.
2. **Environmental Testing**: Resistors are subjected to environmental tests, including humidity, temperature cycling, and vibration, to ensure they can withstand real-world conditions.
3. **Calibration Procedures**: Precision resistors are calibrated against known standards to ensure their accuracy and reliability.
V. Challenges in Resistor Production
Despite advancements in technology, resistor production faces several challenges:
A. Tolerance and Precision
Achieving tight tolerances and high precision in resistor manufacturing is critical, especially for applications in measurement and calibration. Variations in raw materials and manufacturing processes can impact the final product's performance.
B. Temperature Coefficients
Resistors must maintain stable resistance values across varying temperatures. Manufacturers must carefully select materials and design processes to minimize temperature coefficients.
C. Material Availability and Cost
The availability and cost of raw materials can fluctuate, impacting production costs and timelines. Manufacturers must navigate these challenges to maintain competitive pricing and quality.
VI. Innovations in Resistor Production
The resistor production industry is continually evolving, with innovations aimed at improving efficiency, quality, and sustainability.
A. Advances in Materials Science
Research into new materials and composites is leading to the development of resistors with enhanced performance characteristics, such as improved temperature stability and lower noise levels.
B. Automation and Industry 4.0
The integration of automation and smart manufacturing technologies is streamlining production processes, reducing labor costs, and increasing production efficiency.
C. Sustainable Practices in Production
Manufacturers are increasingly adopting sustainable practices, such as recycling materials and reducing waste, to minimize their environmental impact.
VII. Conclusion
In summary, the production of resistor standards is a complex process that involves various types of resistors, raw materials, and manufacturing techniques. The challenges faced in achieving precision and reliability are met with ongoing innovations in materials science and production methods. As technology continues to advance, the role of resistor standards in electronics will remain vital, ensuring the performance and reliability of electronic devices across industries.
VIII. References
A comprehensive list of academic journals, industry reports, and publications from standards organizations can provide further insights into the production processes and innovations in resistor standards. These resources are invaluable for anyone looking to deepen their understanding of this critical component in electronics.