What are the Manufacturing Processes of the Latest Resistor Wiring Diagrams?
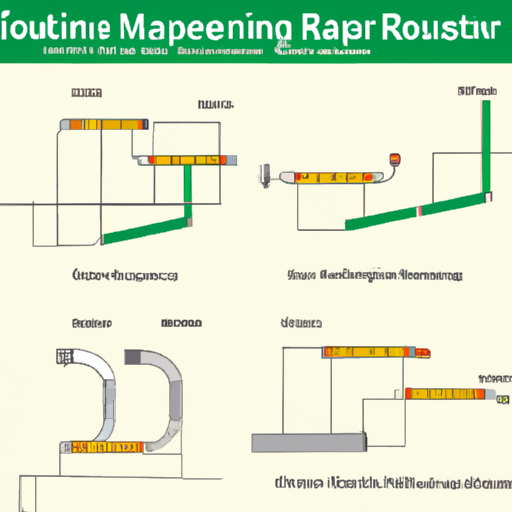
I. Introduction
Resistors are fundamental components in electronic circuits, serving the crucial role of controlling current flow and voltage levels. They are essential for ensuring that electronic devices function correctly and safely. As technology advances, the complexity and precision of resistor wiring diagrams have evolved, reflecting the need for more sophisticated manufacturing processes. This article aims to explore the manufacturing processes behind the latest resistor wiring diagrams, shedding light on the intricate steps involved in bringing these essential components to life.
II. Understanding Resistors
A. Types of Resistors
Resistors come in various types, each designed for specific applications:
1. **Fixed Resistors**: These resistors have a constant resistance value and are widely used in circuits where precise resistance is required.
2. **Variable Resistors**: Also known as potentiometers, these allow users to adjust resistance levels, making them ideal for applications like volume controls in audio equipment.
3. **Specialty Resistors**: This category includes thermistors, photoresistors, and others that respond to environmental changes, providing unique functionalities in various applications.
B. Basic Principles of Resistance and Ohm's Law
The behavior of resistors is governed by Ohm's Law, which states that the current (I) flowing through a conductor between two points is directly proportional to the voltage (V) across the two points and inversely proportional to the resistance (R). This relationship is fundamental in designing circuits and understanding how resistors interact with other components.
C. Applications of Resistors in Electronic Devices
Resistors are ubiquitous in electronic devices, from simple household appliances to complex computing systems. They are used in voltage dividers, current limiters, and signal conditioning circuits, playing a vital role in ensuring the reliability and functionality of electronic systems.
III. The Role of Wiring Diagrams
A. Definition and Purpose of Wiring Diagrams
Wiring diagrams are visual representations of electrical circuits, illustrating how components are interconnected. They serve as essential tools for engineers and technicians, providing a clear understanding of circuit design and functionality.
B. Importance of Accurate Wiring Diagrams in Manufacturing and Assembly
Accurate wiring diagrams are critical in the manufacturing process, as they guide assembly workers in connecting components correctly. Errors in wiring can lead to malfunctioning devices, increased production costs, and safety hazards.
C. Components Typically Included in Resistor Wiring Diagrams
A typical resistor wiring diagram includes symbols for resistors, power sources, and other components, along with lines representing electrical connections. These diagrams may also indicate values, tolerances, and other specifications necessary for proper assembly.
IV. Overview of Manufacturing Processes
A. Design and Prototyping
1. Initial Design Considerations
The manufacturing process begins with the design phase, where engineers consider factors such as resistance values, power ratings, and physical dimensions. These considerations are crucial for ensuring that the resistor meets the intended application requirements.
2. Software Tools Used for Creating Wiring Diagrams
Modern design relies heavily on software tools like CAD (Computer-Aided Design) programs, which allow engineers to create precise wiring diagrams and simulate circuit behavior before physical production begins.
3. Prototyping Techniques
Prototyping is an essential step in the design process, enabling engineers to test and refine their designs. Techniques such as 3D printing and breadboarding allow for rapid iteration and validation of resistor designs.
B. Material Selection
1. Common Materials Used in Resistors
The choice of materials significantly impacts the performance and reliability of resistors. Common materials include carbon, metal film, and wire-wound elements, each offering distinct advantages in terms of stability, temperature coefficient, and noise characteristics.
2. Factors Influencing Material Choice
Material selection is influenced by factors such as cost, availability, and the specific electrical and thermal properties required for the application. Engineers must balance these factors to optimize performance while minimizing production costs.
C. Production Techniques
1. Automated vs. Manual Assembly
The production of resistors can be carried out through automated or manual assembly processes. Automated assembly is often preferred for high-volume production, as it increases efficiency and reduces the likelihood of human error.
2. Soldering Methods
Soldering is a critical step in the assembly of resistors into circuits. Common methods include:
Wave Soldering: A process where a wave of molten solder is passed over a circuit board, allowing components to be soldered simultaneously.
Reflow Soldering: Involves applying solder paste to the circuit board, followed by heating to melt the solder and create connections.
3. Surface Mount Technology (SMT) vs. Through-Hole Technology
Surface mount technology (SMT) has gained popularity due to its ability to accommodate smaller components and higher circuit densities. In contrast, through-hole technology, where components are inserted into holes on a circuit board, is still used for specific applications requiring greater mechanical strength.
D. Quality Control
1. Testing Methods for Resistors
Quality control is paramount in resistor manufacturing. Testing methods include:
Resistance Measurement: Ensuring that the resistor meets specified resistance values.
Temperature Coefficient Testing: Evaluating how resistance changes with temperature.
Voltage Rating Tests: Confirming that resistors can handle specified voltage levels without failure.
2. Importance of Quality Assurance in Manufacturing
Quality assurance processes help identify defects early in production, reducing waste and ensuring that only reliable components reach the market. This is crucial for maintaining the integrity of electronic devices.
V. Latest Trends in Resistor Manufacturing
A. Advances in Materials Science
1. Development of New Resistor Materials
Recent advancements in materials science have led to the development of new resistor materials that offer improved performance characteristics, such as higher stability and lower noise levels.
2. Impact on Performance and Reliability
These new materials enhance the reliability and longevity of resistors, making them suitable for demanding applications in industries such as automotive and aerospace.
B. Automation and Industry 4.0
1. Role of Robotics and AI in Manufacturing
The integration of robotics and artificial intelligence (AI) in manufacturing processes has revolutionized resistor production. Automated systems can perform tasks with precision and speed, reducing labor costs and increasing output.
2. Benefits of Smart Manufacturing Systems
Smart manufacturing systems enable real-time monitoring and data analysis, allowing manufacturers to optimize processes, predict maintenance needs, and improve overall efficiency.
C. Environmental Considerations
1. Sustainable Practices in Resistor Manufacturing
As environmental concerns grow, manufacturers are adopting sustainable practices, such as reducing energy consumption and minimizing waste during production.
2. Recycling and Waste Management
Efforts to recycle materials and manage waste effectively are becoming standard practices in the industry, contributing to a more sustainable manufacturing ecosystem.
VI. Case Studies
A. Example of a Modern Resistor Manufacturing Facility
A leading resistor manufacturer has implemented advanced automation and quality control measures, resulting in a significant reduction in production time and an increase in product reliability. Their facility utilizes state-of-the-art robotics for assembly and testing, ensuring that each resistor meets stringent quality standards.
B. Analysis of a Specific Resistor Product and Its Wiring Diagram
Consider a high-precision metal film resistor used in medical devices. Its wiring diagram illustrates the careful arrangement of components to minimize noise and ensure accurate performance. The manufacturing process for this resistor involves meticulous material selection and rigorous testing to meet the demanding requirements of the medical industry.
C. Lessons Learned from Industry Leaders
Industry leaders emphasize the importance of continuous improvement and innovation in manufacturing processes. By adopting new technologies and materials, they can enhance product performance and maintain a competitive edge in the market.
VII. Conclusion
In summary, the manufacturing processes behind the latest resistor wiring diagrams are complex and multifaceted, involving careful design, material selection, and quality control. As technology continues to evolve, so too will the methods used to produce these essential components. Understanding these processes is crucial for anyone involved in electronics, as it highlights the importance of precision and reliability in the design and manufacturing of electronic devices.
The future of resistor manufacturing will likely see further advancements in materials science, automation, and sustainable practices, ensuring that resistors continue to play a vital role in the ever-evolving landscape of electronics.
VIII. References
- Academic papers and articles on resistor technology and manufacturing processes.
- Industry standards and guidelines related to resistor manufacturing and wiring diagrams.
- Resources for further reading on advancements in materials science and automation in manufacturing.
By exploring these topics, readers can gain a deeper understanding of the intricacies involved in resistor manufacturing and the significance of wiring diagrams in the production process.
What are the Manufacturing Processes of the Latest Resistor Wiring Diagrams?
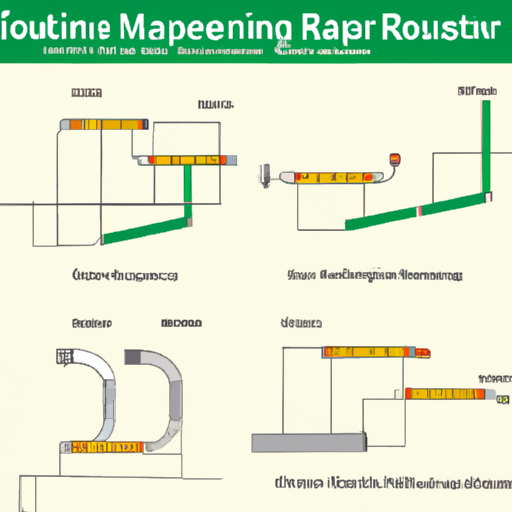
I. Introduction
Resistors are fundamental components in electronic circuits, serving the crucial role of controlling current flow and voltage levels. They are essential for ensuring that electronic devices function correctly and safely. As technology advances, the complexity and precision of resistor wiring diagrams have evolved, reflecting the need for more sophisticated manufacturing processes. This article aims to explore the manufacturing processes behind the latest resistor wiring diagrams, shedding light on the intricate steps involved in bringing these essential components to life.
II. Understanding Resistors
A. Types of Resistors
Resistors come in various types, each designed for specific applications:
1. **Fixed Resistors**: These resistors have a constant resistance value and are widely used in circuits where precise resistance is required.
2. **Variable Resistors**: Also known as potentiometers, these allow users to adjust resistance levels, making them ideal for applications like volume controls in audio equipment.
3. **Specialty Resistors**: This category includes thermistors, photoresistors, and others that respond to environmental changes, providing unique functionalities in various applications.
B. Basic Principles of Resistance and Ohm's Law
The behavior of resistors is governed by Ohm's Law, which states that the current (I) flowing through a conductor between two points is directly proportional to the voltage (V) across the two points and inversely proportional to the resistance (R). This relationship is fundamental in designing circuits and understanding how resistors interact with other components.
C. Applications of Resistors in Electronic Devices
Resistors are ubiquitous in electronic devices, from simple household appliances to complex computing systems. They are used in voltage dividers, current limiters, and signal conditioning circuits, playing a vital role in ensuring the reliability and functionality of electronic systems.
III. The Role of Wiring Diagrams
A. Definition and Purpose of Wiring Diagrams
Wiring diagrams are visual representations of electrical circuits, illustrating how components are interconnected. They serve as essential tools for engineers and technicians, providing a clear understanding of circuit design and functionality.
B. Importance of Accurate Wiring Diagrams in Manufacturing and Assembly
Accurate wiring diagrams are critical in the manufacturing process, as they guide assembly workers in connecting components correctly. Errors in wiring can lead to malfunctioning devices, increased production costs, and safety hazards.
C. Components Typically Included in Resistor Wiring Diagrams
A typical resistor wiring diagram includes symbols for resistors, power sources, and other components, along with lines representing electrical connections. These diagrams may also indicate values, tolerances, and other specifications necessary for proper assembly.
IV. Overview of Manufacturing Processes
A. Design and Prototyping
1. Initial Design Considerations
The manufacturing process begins with the design phase, where engineers consider factors such as resistance values, power ratings, and physical dimensions. These considerations are crucial for ensuring that the resistor meets the intended application requirements.
2. Software Tools Used for Creating Wiring Diagrams
Modern design relies heavily on software tools like CAD (Computer-Aided Design) programs, which allow engineers to create precise wiring diagrams and simulate circuit behavior before physical production begins.
3. Prototyping Techniques
Prototyping is an essential step in the design process, enabling engineers to test and refine their designs. Techniques such as 3D printing and breadboarding allow for rapid iteration and validation of resistor designs.
B. Material Selection
1. Common Materials Used in Resistors
The choice of materials significantly impacts the performance and reliability of resistors. Common materials include carbon, metal film, and wire-wound elements, each offering distinct advantages in terms of stability, temperature coefficient, and noise characteristics.
2. Factors Influencing Material Choice
Material selection is influenced by factors such as cost, availability, and the specific electrical and thermal properties required for the application. Engineers must balance these factors to optimize performance while minimizing production costs.
C. Production Techniques
1. Automated vs. Manual Assembly
The production of resistors can be carried out through automated or manual assembly processes. Automated assembly is often preferred for high-volume production, as it increases efficiency and reduces the likelihood of human error.
2. Soldering Methods
Soldering is a critical step in the assembly of resistors into circuits. Common methods include:
Wave Soldering: A process where a wave of molten solder is passed over a circuit board, allowing components to be soldered simultaneously.
Reflow Soldering: Involves applying solder paste to the circuit board, followed by heating to melt the solder and create connections.
3. Surface Mount Technology (SMT) vs. Through-Hole Technology
Surface mount technology (SMT) has gained popularity due to its ability to accommodate smaller components and higher circuit densities. In contrast, through-hole technology, where components are inserted into holes on a circuit board, is still used for specific applications requiring greater mechanical strength.
D. Quality Control
1. Testing Methods for Resistors
Quality control is paramount in resistor manufacturing. Testing methods include:
Resistance Measurement: Ensuring that the resistor meets specified resistance values.
Temperature Coefficient Testing: Evaluating how resistance changes with temperature.
Voltage Rating Tests: Confirming that resistors can handle specified voltage levels without failure.
2. Importance of Quality Assurance in Manufacturing
Quality assurance processes help identify defects early in production, reducing waste and ensuring that only reliable components reach the market. This is crucial for maintaining the integrity of electronic devices.
V. Latest Trends in Resistor Manufacturing
A. Advances in Materials Science
1. Development of New Resistor Materials
Recent advancements in materials science have led to the development of new resistor materials that offer improved performance characteristics, such as higher stability and lower noise levels.
2. Impact on Performance and Reliability
These new materials enhance the reliability and longevity of resistors, making them suitable for demanding applications in industries such as automotive and aerospace.
B. Automation and Industry 4.0
1. Role of Robotics and AI in Manufacturing
The integration of robotics and artificial intelligence (AI) in manufacturing processes has revolutionized resistor production. Automated systems can perform tasks with precision and speed, reducing labor costs and increasing output.
2. Benefits of Smart Manufacturing Systems
Smart manufacturing systems enable real-time monitoring and data analysis, allowing manufacturers to optimize processes, predict maintenance needs, and improve overall efficiency.
C. Environmental Considerations
1. Sustainable Practices in Resistor Manufacturing
As environmental concerns grow, manufacturers are adopting sustainable practices, such as reducing energy consumption and minimizing waste during production.
2. Recycling and Waste Management
Efforts to recycle materials and manage waste effectively are becoming standard practices in the industry, contributing to a more sustainable manufacturing ecosystem.
VI. Case Studies
A. Example of a Modern Resistor Manufacturing Facility
A leading resistor manufacturer has implemented advanced automation and quality control measures, resulting in a significant reduction in production time and an increase in product reliability. Their facility utilizes state-of-the-art robotics for assembly and testing, ensuring that each resistor meets stringent quality standards.
B. Analysis of a Specific Resistor Product and Its Wiring Diagram
Consider a high-precision metal film resistor used in medical devices. Its wiring diagram illustrates the careful arrangement of components to minimize noise and ensure accurate performance. The manufacturing process for this resistor involves meticulous material selection and rigorous testing to meet the demanding requirements of the medical industry.
C. Lessons Learned from Industry Leaders
Industry leaders emphasize the importance of continuous improvement and innovation in manufacturing processes. By adopting new technologies and materials, they can enhance product performance and maintain a competitive edge in the market.
VII. Conclusion
In summary, the manufacturing processes behind the latest resistor wiring diagrams are complex and multifaceted, involving careful design, material selection, and quality control. As technology continues to evolve, so too will the methods used to produce these essential components. Understanding these processes is crucial for anyone involved in electronics, as it highlights the importance of precision and reliability in the design and manufacturing of electronic devices.
The future of resistor manufacturing will likely see further advancements in materials science, automation, and sustainable practices, ensuring that resistors continue to play a vital role in the ever-evolving landscape of electronics.
VIII. References
- Academic papers and articles on resistor technology and manufacturing processes.
- Industry standards and guidelines related to resistor manufacturing and wiring diagrams.
- Resources for further reading on advancements in materials science and automation in manufacturing.
By exploring these topics, readers can gain a deeper understanding of the intricacies involved in resistor manufacturing and the significance of wiring diagrams in the production process.