The Production Process of Mainstream Power Wire-Winding Resistors
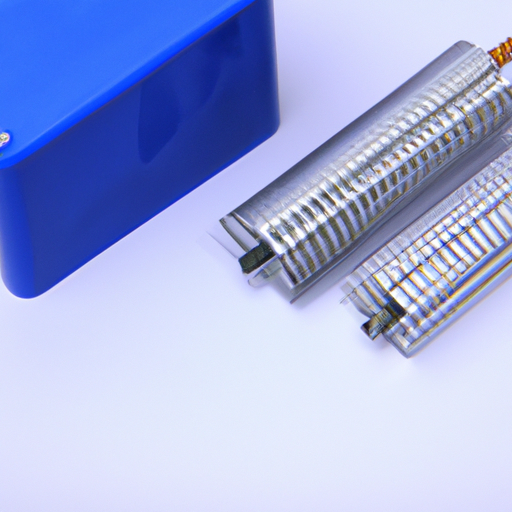
I. Introduction
Power wire-winding resistors are essential components in various electrical applications, serving as crucial elements in power management, energy dissipation, and circuit protection. These resistors are designed to handle high power levels and are widely used in industries ranging from automotive to telecommunications. Understanding the production process of these resistors is vital for engineers, manufacturers, and anyone interested in the electronics field. This blog post will delve into the materials, design considerations, and detailed steps involved in the production of mainstream power wire-winding resistors.
II. Materials Used in Power Wire-Winding Resistors
A. Types of Wire Materials
The choice of wire material is critical in determining the performance and reliability of power wire-winding resistors. The most commonly used materials include:
1. **Nickel-Chromium Alloys**: Known for their excellent resistance to oxidation and high-temperature stability, nickel-chromium alloys are often used in high-power applications. They provide a stable resistance value and can withstand significant thermal stress.
2. **Copper-Nickel Alloys**: These alloys offer good conductivity and thermal performance, making them suitable for applications where efficiency is paramount. They are often used in lower power applications but can still handle substantial loads.
B. Insulating Materials
Insulation is crucial for ensuring the safety and functionality of wire-winding resistors. The most common insulating materials include:
1. **Ceramic**: Ceramic materials are favored for their high thermal resistance and electrical insulation properties. They can withstand high temperatures without degrading, making them ideal for high-power applications.
2. **Epoxy Resins**: These resins provide excellent electrical insulation and mechanical strength. They are often used in conjunction with other materials to enhance the durability and performance of the resistors.
C. Other Components
In addition to wire and insulation, several other components are essential in the production of power wire-winding resistors:
1. **End Caps**: These components are used to secure the ends of the resistor and provide a connection point for electrical terminals.
2. **Heat Sinks**: To manage the heat generated during operation, heat sinks are often integrated into the design. They help dissipate heat away from the resistor, ensuring stable performance.
III. Design Considerations
A. Resistance Value Calculation
The resistance value is a fundamental parameter that must be calculated based on the application requirements. This involves determining the desired current and voltage levels, which will dictate the resistance needed to achieve the desired power dissipation.
B. Power Rating and Thermal Management
Power rating is another critical consideration. It defines the maximum power the resistor can handle without overheating. Effective thermal management strategies, such as using heat sinks or selecting appropriate materials, are essential to ensure the resistor operates within safe temperature limits.
C. Physical Dimensions and Form Factor
The physical dimensions of the resistor must be designed to fit within the constraints of the application. This includes considerations for space, mounting options, and overall form factor, which can affect both performance and integration into electronic systems.
D. Tolerance and Stability Requirements
Tolerance refers to the allowable deviation from the specified resistance value. High-stability resistors are often required in precision applications, necessitating careful selection of materials and manufacturing processes to ensure consistent performance.
IV. The Production Process
The production of power wire-winding resistors involves several key steps, each critical to ensuring the final product meets the required specifications.
A. Wire Preparation
1. **Wire Sizing and Cutting**: The first step in the production process is preparing the wire. This involves cutting the wire to the desired length based on the calculated resistance value and the design specifications.
2. **Surface Treatment**: To enhance adhesion and improve electrical properties, the wire undergoes surface treatment. This may include cleaning, coating, or other processes to ensure optimal performance.
B. Winding Process
1. **Winding Techniques**: The wire is then wound onto a core or substrate using various techniques. The winding process can be done manually or with automated machinery, depending on the scale of production.
2. **Layering and Spacing**: Proper layering and spacing of the wire are crucial to achieving the desired resistance value and ensuring effective heat dissipation. This step requires precision to maintain consistent performance.
C. Insulation Application
1. **Insulation Types and Methods**: After winding, insulation is applied to the resistor. This can involve dipping the wound resistor in epoxy resin or applying ceramic insulation. The choice of insulation method depends on the desired properties and application requirements.
2. **Curing Processes**: Once the insulation is applied, it must be cured to achieve the desired mechanical and electrical properties. Curing can involve heat treatment or chemical processes, depending on the materials used.
D. Assembly
1. **Mounting on Substrates**: The insulated resistor is then mounted on a substrate, which may include additional components such as heat sinks or end caps. This step is crucial for ensuring the resistor is securely integrated into the final product.
2. **Integration of Additional Components**: Additional components, such as terminals and connectors, are integrated during the assembly process. This ensures that the resistor can be easily connected to the electrical circuit.
E. Testing and Quality Control
1. **Electrical Testing**: Once assembled, the resistors undergo rigorous electrical testing to verify their performance. This includes measuring resistance values, power ratings, and ensuring they meet specified tolerances.
2. **Thermal Testing**: Thermal testing is conducted to assess the resistor's performance under load conditions. This helps identify any potential overheating issues and ensures the resistor can handle the required power levels.
3. **Visual Inspection**: A final visual inspection is performed to check for any defects or inconsistencies in the manufacturing process. This step is crucial for maintaining quality standards.
V. Finalization and Packaging
A. Final Assembly
After passing all tests, the resistors undergo final assembly, which may include additional protective coatings or labeling. This ensures that the product is ready for distribution and use.
B. Packaging Considerations
Proper packaging is essential to protect the resistors during shipping and handling. Packaging materials must be chosen to prevent damage and ensure the resistors remain in optimal condition until they reach the end user.
C. Shipping and Distribution
Once packaged, the resistors are prepared for shipping and distribution. This involves coordinating logistics to ensure timely delivery to customers and maintaining inventory levels.
VI. Conclusion
The production process of mainstream power wire-winding resistors is a complex and meticulous endeavor that requires careful consideration of materials, design, and manufacturing techniques. Each step, from wire preparation to final testing, plays a crucial role in ensuring the quality and reliability of the final product. As technology continues to evolve, the demand for high-performance resistors will only increase, driving innovations in production methods and materials. Quality control remains paramount in this industry, ensuring that every resistor meets the stringent requirements of modern electrical applications. Understanding this production process not only highlights the intricacies involved but also underscores the importance of these components in the broader context of electrical engineering and technology.
VII. References
- Academic Journals on Electrical Engineering
- Industry Standards for Resistor Manufacturing
- Manufacturer Guidelines for Power Wire-Winding Resistors
This comprehensive overview of the production process of power wire-winding resistors provides valuable insights into the complexities and considerations involved in creating these essential components. Whether you are an engineer, a manufacturer, or simply an enthusiast, understanding this process can enhance your appreciation for the technology that powers our modern world.
The Production Process of Mainstream Power Wire-Winding Resistors
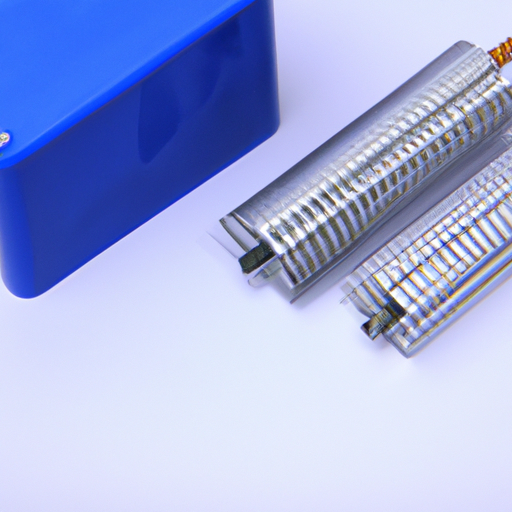
I. Introduction
Power wire-winding resistors are essential components in various electrical applications, serving as crucial elements in power management, energy dissipation, and circuit protection. These resistors are designed to handle high power levels and are widely used in industries ranging from automotive to telecommunications. Understanding the production process of these resistors is vital for engineers, manufacturers, and anyone interested in the electronics field. This blog post will delve into the materials, design considerations, and detailed steps involved in the production of mainstream power wire-winding resistors.
II. Materials Used in Power Wire-Winding Resistors
A. Types of Wire Materials
The choice of wire material is critical in determining the performance and reliability of power wire-winding resistors. The most commonly used materials include:
1. **Nickel-Chromium Alloys**: Known for their excellent resistance to oxidation and high-temperature stability, nickel-chromium alloys are often used in high-power applications. They provide a stable resistance value and can withstand significant thermal stress.
2. **Copper-Nickel Alloys**: These alloys offer good conductivity and thermal performance, making them suitable for applications where efficiency is paramount. They are often used in lower power applications but can still handle substantial loads.
B. Insulating Materials
Insulation is crucial for ensuring the safety and functionality of wire-winding resistors. The most common insulating materials include:
1. **Ceramic**: Ceramic materials are favored for their high thermal resistance and electrical insulation properties. They can withstand high temperatures without degrading, making them ideal for high-power applications.
2. **Epoxy Resins**: These resins provide excellent electrical insulation and mechanical strength. They are often used in conjunction with other materials to enhance the durability and performance of the resistors.
C. Other Components
In addition to wire and insulation, several other components are essential in the production of power wire-winding resistors:
1. **End Caps**: These components are used to secure the ends of the resistor and provide a connection point for electrical terminals.
2. **Heat Sinks**: To manage the heat generated during operation, heat sinks are often integrated into the design. They help dissipate heat away from the resistor, ensuring stable performance.
III. Design Considerations
A. Resistance Value Calculation
The resistance value is a fundamental parameter that must be calculated based on the application requirements. This involves determining the desired current and voltage levels, which will dictate the resistance needed to achieve the desired power dissipation.
B. Power Rating and Thermal Management
Power rating is another critical consideration. It defines the maximum power the resistor can handle without overheating. Effective thermal management strategies, such as using heat sinks or selecting appropriate materials, are essential to ensure the resistor operates within safe temperature limits.
C. Physical Dimensions and Form Factor
The physical dimensions of the resistor must be designed to fit within the constraints of the application. This includes considerations for space, mounting options, and overall form factor, which can affect both performance and integration into electronic systems.
D. Tolerance and Stability Requirements
Tolerance refers to the allowable deviation from the specified resistance value. High-stability resistors are often required in precision applications, necessitating careful selection of materials and manufacturing processes to ensure consistent performance.
IV. The Production Process
The production of power wire-winding resistors involves several key steps, each critical to ensuring the final product meets the required specifications.
A. Wire Preparation
1. **Wire Sizing and Cutting**: The first step in the production process is preparing the wire. This involves cutting the wire to the desired length based on the calculated resistance value and the design specifications.
2. **Surface Treatment**: To enhance adhesion and improve electrical properties, the wire undergoes surface treatment. This may include cleaning, coating, or other processes to ensure optimal performance.
B. Winding Process
1. **Winding Techniques**: The wire is then wound onto a core or substrate using various techniques. The winding process can be done manually or with automated machinery, depending on the scale of production.
2. **Layering and Spacing**: Proper layering and spacing of the wire are crucial to achieving the desired resistance value and ensuring effective heat dissipation. This step requires precision to maintain consistent performance.
C. Insulation Application
1. **Insulation Types and Methods**: After winding, insulation is applied to the resistor. This can involve dipping the wound resistor in epoxy resin or applying ceramic insulation. The choice of insulation method depends on the desired properties and application requirements.
2. **Curing Processes**: Once the insulation is applied, it must be cured to achieve the desired mechanical and electrical properties. Curing can involve heat treatment or chemical processes, depending on the materials used.
D. Assembly
1. **Mounting on Substrates**: The insulated resistor is then mounted on a substrate, which may include additional components such as heat sinks or end caps. This step is crucial for ensuring the resistor is securely integrated into the final product.
2. **Integration of Additional Components**: Additional components, such as terminals and connectors, are integrated during the assembly process. This ensures that the resistor can be easily connected to the electrical circuit.
E. Testing and Quality Control
1. **Electrical Testing**: Once assembled, the resistors undergo rigorous electrical testing to verify their performance. This includes measuring resistance values, power ratings, and ensuring they meet specified tolerances.
2. **Thermal Testing**: Thermal testing is conducted to assess the resistor's performance under load conditions. This helps identify any potential overheating issues and ensures the resistor can handle the required power levels.
3. **Visual Inspection**: A final visual inspection is performed to check for any defects or inconsistencies in the manufacturing process. This step is crucial for maintaining quality standards.
V. Finalization and Packaging
A. Final Assembly
After passing all tests, the resistors undergo final assembly, which may include additional protective coatings or labeling. This ensures that the product is ready for distribution and use.
B. Packaging Considerations
Proper packaging is essential to protect the resistors during shipping and handling. Packaging materials must be chosen to prevent damage and ensure the resistors remain in optimal condition until they reach the end user.
C. Shipping and Distribution
Once packaged, the resistors are prepared for shipping and distribution. This involves coordinating logistics to ensure timely delivery to customers and maintaining inventory levels.
VI. Conclusion
The production process of mainstream power wire-winding resistors is a complex and meticulous endeavor that requires careful consideration of materials, design, and manufacturing techniques. Each step, from wire preparation to final testing, plays a crucial role in ensuring the quality and reliability of the final product. As technology continues to evolve, the demand for high-performance resistors will only increase, driving innovations in production methods and materials. Quality control remains paramount in this industry, ensuring that every resistor meets the stringent requirements of modern electrical applications. Understanding this production process not only highlights the intricacies involved but also underscores the importance of these components in the broader context of electrical engineering and technology.
VII. References
- Academic Journals on Electrical Engineering
- Industry Standards for Resistor Manufacturing
- Manufacturer Guidelines for Power Wire-Winding Resistors
This comprehensive overview of the production process of power wire-winding resistors provides valuable insights into the complexities and considerations involved in creating these essential components. Whether you are an engineer, a manufacturer, or simply an enthusiast, understanding this process can enhance your appreciation for the technology that powers our modern world.