What are the Product Standards for Capacitor Formulas?
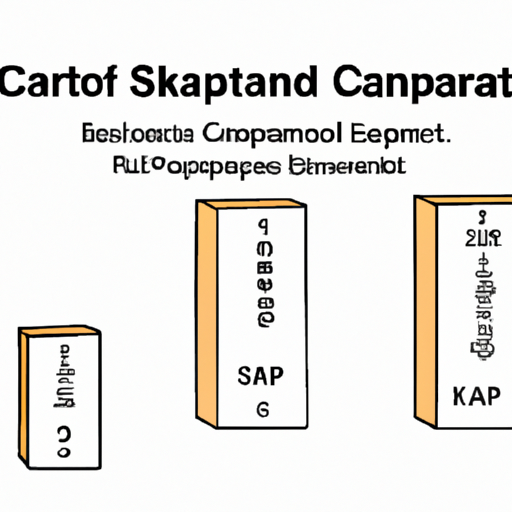
I. Introduction
Capacitors are fundamental components in electronic circuits, serving as energy storage devices that can release energy when needed. They play a crucial role in various applications, from power supply smoothing to signal coupling and filtering. Given their importance, product standards in capacitor manufacturing are vital to ensure safety, reliability, and performance. This blog post aims to explore the product standards for capacitor formulas, highlighting their significance, key organizations involved, common standards, testing methods, challenges, and future trends.
II. Understanding Capacitors
A. Basic Principles of Capacitors
Capacitors function by storing electrical energy in an electric field, created between two conductive plates separated by an insulating material known as a dielectric. When voltage is applied, the capacitor charges, and when the circuit requires energy, it discharges. Capacitors are widely used in various applications, including power electronics, audio equipment, and telecommunications.
B. Types of Capacitors
There are several types of capacitors, each with unique characteristics and applications:
1. **Ceramic Capacitors**: Known for their small size and high stability, ceramic capacitors are commonly used in high-frequency applications.
2. **Electrolytic Capacitors**: These capacitors offer high capacitance values and are often used in power supply circuits.
3. **Film Capacitors**: Made from thin plastic films, these capacitors are known for their reliability and are used in audio and power applications.
C. Key Parameters of Capacitors
Understanding the key parameters of capacitors is essential for selecting the right component for a specific application:
1. **Capacitance**: Measured in farads (F), capacitance indicates the amount of charge a capacitor can store.
2. **Voltage Rating**: This parameter specifies the maximum voltage a capacitor can handle without failure.
3. **Tolerance**: Tolerance indicates the permissible variation in capacitance, expressed as a percentage.
4. **Temperature Coefficient**: This parameter describes how capacitance changes with temperature, which is crucial for applications in varying thermal environments.
III. Importance of Product Standards
A. Ensuring Safety and Reliability
Product standards are essential for ensuring that capacitors operate safely and reliably under specified conditions. Adhering to these standards minimizes the risk of failures that could lead to equipment damage or safety hazards.
B. Facilitating Compatibility and Interoperability
Standards promote compatibility and interoperability among different manufacturers' products. This is particularly important in industries where components from various suppliers must work together seamlessly.
C. Enhancing Performance and Longevity
By following established standards, manufacturers can enhance the performance and longevity of their capacitors. This leads to improved efficiency and reduced maintenance costs for end-users.
D. Regulatory Compliance and Market Access
Compliance with product standards is often a prerequisite for market access. Regulatory bodies require manufacturers to meet specific standards to ensure that their products are safe and environmentally friendly.
IV. Key Standards Organizations
Several organizations play a crucial role in developing and maintaining product standards for capacitors:
A. International Electrotechnical Commission (IEC)
The IEC is a global organization that prepares and publishes international standards for electrical and electronic technologies. Their standards for capacitors cover various aspects, including safety, performance, and testing methods.
B. Institute of Electrical and Electronics Engineers (IEEE)
IEEE develops standards that address the electrical and electronic engineering fields. Their standards relevant to capacitors focus on performance criteria and testing methods.
C. American National Standards Institute (ANSI)
ANSI oversees the development of voluntary consensus standards for products, services, processes, and systems in the United States. Their standards help ensure quality and safety in capacitor manufacturing.
D. Other Relevant Organizations
Organizations such as Underwriters Laboratories (UL) and the Restriction of Hazardous Substances (RoHS) directive also play significant roles in establishing safety and environmental standards for capacitors.
V. Common Product Standards for Capacitors
Several key standards govern the manufacturing and testing of capacitors:
A. IEC 60384 - Fixed Capacitors for Use in Electronic Equipment
This standard specifies the requirements for fixed capacitors used in electronic equipment, including performance, safety, and testing methods.
B. IEC 61071 - Capacitors for Power Electronics
IEC 61071 outlines the requirements for capacitors used in power electronic applications, focusing on performance and reliability under high-stress conditions.
C. MIL-PRF-39014 - Military Specifications for Capacitors
This military standard provides specifications for capacitors used in military applications, ensuring high reliability and performance in demanding environments.
D. ISO 9001 - Quality Management Systems in Capacitor Manufacturing
ISO 9001 sets the criteria for quality management systems, ensuring that manufacturers consistently produce high-quality capacitors.
E. RoHS and WEEE Directives - Environmental Standards
The RoHS directive restricts the use of hazardous substances in electrical and electronic equipment, while the WEEE directive focuses on the recycling and disposal of electronic waste, promoting environmental sustainability.
VI. Testing and Quality Assurance
A. Importance of Testing in Capacitor Manufacturing
Testing is a critical aspect of capacitor manufacturing, ensuring that products meet specified standards and perform reliably in their intended applications.
B. Common Testing Methods
1. **Capacitance Measurement**: This method assesses the actual capacitance of a capacitor, ensuring it falls within the specified tolerance range.
2. **Insulation Resistance Testing**: This test evaluates the insulation properties of the capacitor, ensuring it can withstand the applied voltage without leakage.
3. **Voltage Withstand Testing**: This test determines the capacitor's ability to handle high voltages without failure.
C. Quality Assurance Processes
Quality assurance processes in capacitor manufacturing include:
1. **Incoming Material Inspection**: Ensuring that raw materials meet specified standards before production begins.
2. **In-Process Quality Control**: Monitoring production processes to identify and rectify issues in real-time.
3. **Final Product Testing**: Conducting comprehensive tests on finished capacitors to ensure they meet all performance and safety standards.
VII. Challenges in Meeting Product Standards
A. Technological Advancements and Evolving Standards
As technology advances, product standards must evolve to keep pace with new materials and applications. Manufacturers face the challenge of adapting to these changes while maintaining compliance.
B. Cost Implications of Compliance
Meeting product standards can involve significant costs, including testing, certification, and potential redesigns. Manufacturers must balance these costs with the need for compliance.
C. Global Variations in Standards
Different regions may have varying standards, complicating the manufacturing process for companies operating internationally. Navigating these differences requires careful planning and resources.
D. Balancing Performance with Regulatory Requirements
Manufacturers must balance the desire for high-performance capacitors with the need to meet regulatory requirements, which can sometimes conflict.
VIII. Future Trends in Capacitor Standards
A. Impact of Emerging Technologies
Emerging technologies, such as electric vehicles and renewable energy systems, are driving changes in capacitor design and performance requirements. Standards will need to adapt to these new applications.
B. Increasing Focus on Sustainability
As environmental concerns grow, there is an increasing focus on sustainability in capacitor manufacturing. Standards will likely evolve to address the environmental impact of materials and production processes.
C. Anticipated Changes in Regulatory Frameworks
Regulatory frameworks are expected to become more stringent, particularly regarding environmental and safety standards. Manufacturers must stay informed and prepared for these changes.
IX. Conclusion
Product standards for capacitors are essential for ensuring safety, reliability, and performance in electronic applications. Manufacturers play a crucial role in adhering to these standards, which not only facilitate market access but also enhance the overall quality of their products. As technology continues to evolve, the landscape of capacitor standards will also change, presenting both challenges and opportunities for the industry. By staying informed and proactive, manufacturers can navigate these changes and contribute to a safer, more efficient electronic future.
X. References
1. IEC 60384 - Fixed Capacitors for Use in Electronic Equipment
2. IEC 61071 - Capacitors for Power Electronics
3. MIL-PRF-39014 - Military Specifications for Capacitors
4. ISO 9001 - Quality Management Systems
5. RoHS Directive
6. WEEE Directive
7. IEEE Standards for Capacitors
8. ANSI Standards for Capacitors
9. UL Standards for Electrical Components
This blog post provides a comprehensive overview of the product standards for capacitor formulas, emphasizing their importance in the manufacturing process and the broader implications for the electronics industry.
What are the Product Standards for Capacitor Formulas?
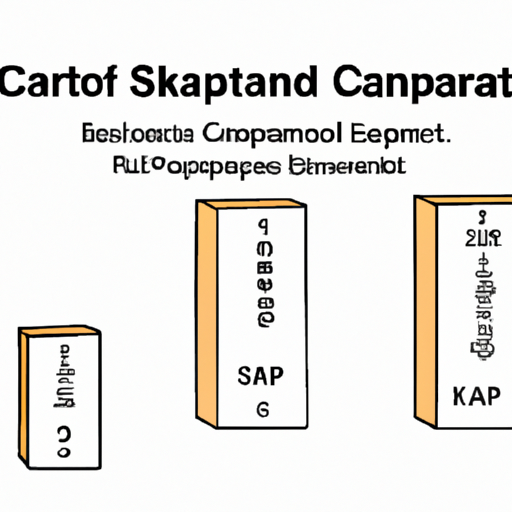
I. Introduction
Capacitors are fundamental components in electronic circuits, serving as energy storage devices that can release energy when needed. They play a crucial role in various applications, from power supply smoothing to signal coupling and filtering. Given their importance, product standards in capacitor manufacturing are vital to ensure safety, reliability, and performance. This blog post aims to explore the product standards for capacitor formulas, highlighting their significance, key organizations involved, common standards, testing methods, challenges, and future trends.
II. Understanding Capacitors
A. Basic Principles of Capacitors
Capacitors function by storing electrical energy in an electric field, created between two conductive plates separated by an insulating material known as a dielectric. When voltage is applied, the capacitor charges, and when the circuit requires energy, it discharges. Capacitors are widely used in various applications, including power electronics, audio equipment, and telecommunications.
B. Types of Capacitors
There are several types of capacitors, each with unique characteristics and applications:
1. **Ceramic Capacitors**: Known for their small size and high stability, ceramic capacitors are commonly used in high-frequency applications.
2. **Electrolytic Capacitors**: These capacitors offer high capacitance values and are often used in power supply circuits.
3. **Film Capacitors**: Made from thin plastic films, these capacitors are known for their reliability and are used in audio and power applications.
C. Key Parameters of Capacitors
Understanding the key parameters of capacitors is essential for selecting the right component for a specific application:
1. **Capacitance**: Measured in farads (F), capacitance indicates the amount of charge a capacitor can store.
2. **Voltage Rating**: This parameter specifies the maximum voltage a capacitor can handle without failure.
3. **Tolerance**: Tolerance indicates the permissible variation in capacitance, expressed as a percentage.
4. **Temperature Coefficient**: This parameter describes how capacitance changes with temperature, which is crucial for applications in varying thermal environments.
III. Importance of Product Standards
A. Ensuring Safety and Reliability
Product standards are essential for ensuring that capacitors operate safely and reliably under specified conditions. Adhering to these standards minimizes the risk of failures that could lead to equipment damage or safety hazards.
B. Facilitating Compatibility and Interoperability
Standards promote compatibility and interoperability among different manufacturers' products. This is particularly important in industries where components from various suppliers must work together seamlessly.
C. Enhancing Performance and Longevity
By following established standards, manufacturers can enhance the performance and longevity of their capacitors. This leads to improved efficiency and reduced maintenance costs for end-users.
D. Regulatory Compliance and Market Access
Compliance with product standards is often a prerequisite for market access. Regulatory bodies require manufacturers to meet specific standards to ensure that their products are safe and environmentally friendly.
IV. Key Standards Organizations
Several organizations play a crucial role in developing and maintaining product standards for capacitors:
A. International Electrotechnical Commission (IEC)
The IEC is a global organization that prepares and publishes international standards for electrical and electronic technologies. Their standards for capacitors cover various aspects, including safety, performance, and testing methods.
B. Institute of Electrical and Electronics Engineers (IEEE)
IEEE develops standards that address the electrical and electronic engineering fields. Their standards relevant to capacitors focus on performance criteria and testing methods.
C. American National Standards Institute (ANSI)
ANSI oversees the development of voluntary consensus standards for products, services, processes, and systems in the United States. Their standards help ensure quality and safety in capacitor manufacturing.
D. Other Relevant Organizations
Organizations such as Underwriters Laboratories (UL) and the Restriction of Hazardous Substances (RoHS) directive also play significant roles in establishing safety and environmental standards for capacitors.
V. Common Product Standards for Capacitors
Several key standards govern the manufacturing and testing of capacitors:
A. IEC 60384 - Fixed Capacitors for Use in Electronic Equipment
This standard specifies the requirements for fixed capacitors used in electronic equipment, including performance, safety, and testing methods.
B. IEC 61071 - Capacitors for Power Electronics
IEC 61071 outlines the requirements for capacitors used in power electronic applications, focusing on performance and reliability under high-stress conditions.
C. MIL-PRF-39014 - Military Specifications for Capacitors
This military standard provides specifications for capacitors used in military applications, ensuring high reliability and performance in demanding environments.
D. ISO 9001 - Quality Management Systems in Capacitor Manufacturing
ISO 9001 sets the criteria for quality management systems, ensuring that manufacturers consistently produce high-quality capacitors.
E. RoHS and WEEE Directives - Environmental Standards
The RoHS directive restricts the use of hazardous substances in electrical and electronic equipment, while the WEEE directive focuses on the recycling and disposal of electronic waste, promoting environmental sustainability.
VI. Testing and Quality Assurance
A. Importance of Testing in Capacitor Manufacturing
Testing is a critical aspect of capacitor manufacturing, ensuring that products meet specified standards and perform reliably in their intended applications.
B. Common Testing Methods
1. **Capacitance Measurement**: This method assesses the actual capacitance of a capacitor, ensuring it falls within the specified tolerance range.
2. **Insulation Resistance Testing**: This test evaluates the insulation properties of the capacitor, ensuring it can withstand the applied voltage without leakage.
3. **Voltage Withstand Testing**: This test determines the capacitor's ability to handle high voltages without failure.
C. Quality Assurance Processes
Quality assurance processes in capacitor manufacturing include:
1. **Incoming Material Inspection**: Ensuring that raw materials meet specified standards before production begins.
2. **In-Process Quality Control**: Monitoring production processes to identify and rectify issues in real-time.
3. **Final Product Testing**: Conducting comprehensive tests on finished capacitors to ensure they meet all performance and safety standards.
VII. Challenges in Meeting Product Standards
A. Technological Advancements and Evolving Standards
As technology advances, product standards must evolve to keep pace with new materials and applications. Manufacturers face the challenge of adapting to these changes while maintaining compliance.
B. Cost Implications of Compliance
Meeting product standards can involve significant costs, including testing, certification, and potential redesigns. Manufacturers must balance these costs with the need for compliance.
C. Global Variations in Standards
Different regions may have varying standards, complicating the manufacturing process for companies operating internationally. Navigating these differences requires careful planning and resources.
D. Balancing Performance with Regulatory Requirements
Manufacturers must balance the desire for high-performance capacitors with the need to meet regulatory requirements, which can sometimes conflict.
VIII. Future Trends in Capacitor Standards
A. Impact of Emerging Technologies
Emerging technologies, such as electric vehicles and renewable energy systems, are driving changes in capacitor design and performance requirements. Standards will need to adapt to these new applications.
B. Increasing Focus on Sustainability
As environmental concerns grow, there is an increasing focus on sustainability in capacitor manufacturing. Standards will likely evolve to address the environmental impact of materials and production processes.
C. Anticipated Changes in Regulatory Frameworks
Regulatory frameworks are expected to become more stringent, particularly regarding environmental and safety standards. Manufacturers must stay informed and prepared for these changes.
IX. Conclusion
Product standards for capacitors are essential for ensuring safety, reliability, and performance in electronic applications. Manufacturers play a crucial role in adhering to these standards, which not only facilitate market access but also enhance the overall quality of their products. As technology continues to evolve, the landscape of capacitor standards will also change, presenting both challenges and opportunities for the industry. By staying informed and proactive, manufacturers can navigate these changes and contribute to a safer, more efficient electronic future.
X. References
1. IEC 60384 - Fixed Capacitors for Use in Electronic Equipment
2. IEC 61071 - Capacitors for Power Electronics
3. MIL-PRF-39014 - Military Specifications for Capacitors
4. ISO 9001 - Quality Management Systems
5. RoHS Directive
6. WEEE Directive
7. IEEE Standards for Capacitors
8. ANSI Standards for Capacitors
9. UL Standards for Electrical Components
This blog post provides a comprehensive overview of the product standards for capacitor formulas, emphasizing their importance in the manufacturing process and the broader implications for the electronics industry.