What are the Product Standards for Film Capacitors?
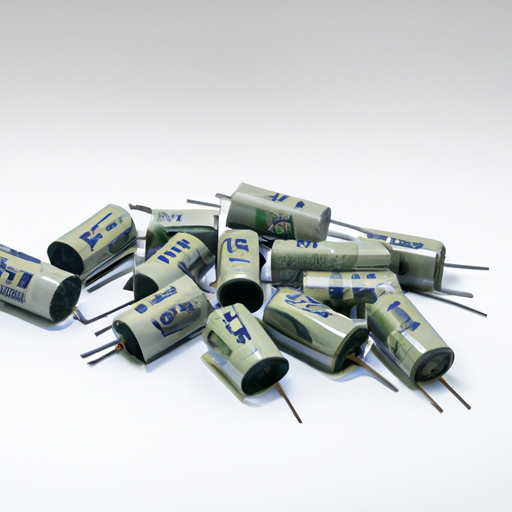
I. Introduction
Film capacitors are essential components in a wide range of electronic devices, from consumer electronics to industrial machinery. These capacitors are known for their reliability, stability, and versatility, making them a popular choice in various applications. However, the effectiveness and safety of film capacitors depend significantly on adherence to established product standards. This article will explore the product standards for film capacitors, their importance, and the challenges manufacturers face in meeting these standards.
II. Understanding Film Capacitors
A. Composition and Structure
Film capacitors consist of a dielectric material sandwiched between two conductive layers. The dielectric materials used can vary, including polyester, polypropylene, and polycarbonate, each offering different electrical properties and performance characteristics. The choice of dielectric material directly influences the capacitor's capacitance, voltage rating, and temperature stability.
1. Dielectric Materials
The dielectric material is crucial in determining the capacitor's performance. For instance, polypropylene film capacitors are known for their low dielectric losses and high insulation resistance, making them suitable for high-frequency applications. In contrast, polyester film capacitors are more cost-effective and widely used in general-purpose applications.
2. Types of Film Capacitors
Film capacitors can be categorized into several types based on their construction and application. Common types include:
Polyester Capacitors: Often used in consumer electronics due to their affordability.
Polypropylene Capacitors: Preferred for high-frequency applications due to their superior performance.
Metalized Film Capacitors: Feature a thin layer of metal deposited on the dielectric, providing self-healing properties.
B. Applications of Film Capacitors
Film capacitors find applications across various sectors, including:
1. Consumer Electronics
In consumer electronics, film capacitors are used in audio equipment, televisions, and power supplies. Their ability to handle high frequencies and provide stable performance makes them ideal for these applications.
2. Industrial Applications
In industrial settings, film capacitors are utilized in motor drives, power converters, and renewable energy systems. Their robustness and reliability are critical in environments where performance is paramount.
3. Automotive and Aerospace
Film capacitors are increasingly used in automotive and aerospace applications, where safety and reliability are non-negotiable. They are employed in power management systems, electronic control units, and safety systems.
III. Importance of Product Standards
A. Ensuring Quality and Reliability
Product standards play a vital role in ensuring the quality and reliability of film capacitors. By adhering to established standards, manufacturers can guarantee that their products meet specific performance criteria, reducing the risk of failure in critical applications.
B. Safety Considerations
Safety is a primary concern in the design and manufacturing of electronic components. Product standards help mitigate risks associated with electrical failures, overheating, and other hazards that could lead to accidents or equipment damage.
C. Regulatory Compliance
Compliance with product standards is often a legal requirement in many regions. Manufacturers must ensure that their products meet local and international regulations to avoid penalties and ensure market access.
D. Market Acceptance and Competitiveness
Products that meet recognized standards are more likely to gain acceptance in the market. Adhering to these standards can enhance a manufacturer's reputation and competitiveness, as customers often prefer products that are certified and reliable.
IV. Key Product Standards for Film Capacitors
A. International Standards
1. IEC (International Electrotechnical Commission)
The IEC sets several standards relevant to film capacitors, including:
IEC 60384 Series: This series outlines the general requirements for fixed capacitors for use in electronic equipment, including film capacitors.
IEC 61071: This standard specifies the requirements for capacitors used in power electronics.
2. ISO (International Organization for Standardization)
ISO 9001: This standard focuses on quality management systems, ensuring that manufacturers maintain consistent quality in their production processes.
B. National Standards
1. ANSI (American National Standards Institute)
ANSI oversees the development of standards in the United States, including those applicable to film capacitors. Compliance with ANSI standards is often required for products sold in the U.S. market.
2. JIS (Japanese Industrial Standards)
JIS standards govern the quality and performance of electronic components in Japan, including film capacitors. Adhering to these standards is crucial for manufacturers targeting the Japanese market.
C. Industry-Specific Standards
1. Automotive Standards (e.g., AEC-Q200)
The AEC-Q200 standard outlines the qualification requirements for passive components used in automotive applications, ensuring that film capacitors can withstand the harsh conditions typical in vehicles.
2. Aerospace Standards (e.g., AS9100)
AS9100 is a widely recognized quality management standard for the aerospace industry. Compliance with this standard is essential for manufacturers supplying components to aerospace applications, including film capacitors.
V. Testing and Certification Processes
A. Types of Tests for Film Capacitors
To ensure compliance with product standards, film capacitors undergo various testing processes, including:
1. Electrical Testing
Electrical tests assess the capacitor's performance characteristics, such as capacitance, voltage rating, and leakage current. These tests ensure that the capacitor operates within specified limits.
2. Environmental Testing
Environmental tests evaluate the capacitor's performance under different conditions, including temperature, humidity, and exposure to chemicals. These tests help determine the capacitor's reliability in real-world applications.
3. Mechanical Testing
Mechanical tests assess the capacitor's durability and resistance to physical stress, such as vibration and shock. These tests are particularly important for applications in automotive and aerospace industries.
B. Certification Bodies
Several organizations provide certification for film capacitors, ensuring compliance with relevant standards:
1. UL (Underwriters Laboratories)
UL is a global safety certification organization that tests and certifies electronic components, including film capacitors, for safety and performance.
2. TUV (Technischer Überwachungsverein)
TUV is a German certification body that provides testing and certification services for various industries, including electronics. Their certification is recognized worldwide.
3. CSA (Canadian Standards Association)
CSA provides certification services for products sold in Canada, ensuring compliance with national safety and performance standards.
VI. Challenges in Meeting Product Standards
A. Technological Advancements
Rapid technological advancements can make it challenging for manufacturers to keep up with evolving standards. As new materials and technologies emerge, standards must be updated to reflect these changes.
B. Material Sourcing and Quality Control
Sourcing high-quality materials is crucial for manufacturing reliable film capacitors. Variability in material quality can lead to inconsistencies in performance, making it difficult to meet standards.
C. Global Supply Chain Issues
Global supply chain disruptions can impact the availability of materials and components needed for manufacturing. These disruptions can hinder a manufacturer's ability to meet production deadlines and maintain compliance with standards.
VII. Future Trends in Film Capacitor Standards
A. Evolving Technologies
As technology continues to evolve, so too will the standards governing film capacitors. Manufacturers must stay informed about emerging technologies and adapt their products accordingly.
B. Sustainability and Environmental Standards
With increasing emphasis on sustainability, future standards may incorporate environmental considerations, such as the use of eco-friendly materials and manufacturing processes.
C. Impact of Digitalization and Smart Technologies
The rise of digitalization and smart technologies will likely influence the development of new standards for film capacitors, particularly in applications related to the Internet of Things (IoT) and smart devices.
VIII. Conclusion
In conclusion, product standards for film capacitors are essential for ensuring quality, safety, and reliability in various applications. These standards not only facilitate regulatory compliance but also enhance market acceptance and competitiveness. As technology evolves, manufacturers must remain vigilant in adapting to new standards and addressing the challenges of material sourcing and global supply chains. By prioritizing compliance and innovation, the film capacitor industry can continue to advance and meet the demands of an ever-changing technological landscape.
IX. References
- IEC 60384 Series: General Requirements for Fixed Capacitors for Use in Electronic Equipment
- ISO 9001: Quality Management Systems
- AEC-Q200: Qualification Requirements for Passive Components
- AS9100: Quality Management Systems for Aerospace
- UL, TUV, and CSA Certification Guidelines
This comprehensive overview of product standards for film capacitors highlights their significance in ensuring the reliability and safety of these critical components in modern electronics. For further information, readers are encouraged to explore the referenced standards and guidelines.
What are the Product Standards for Film Capacitors?
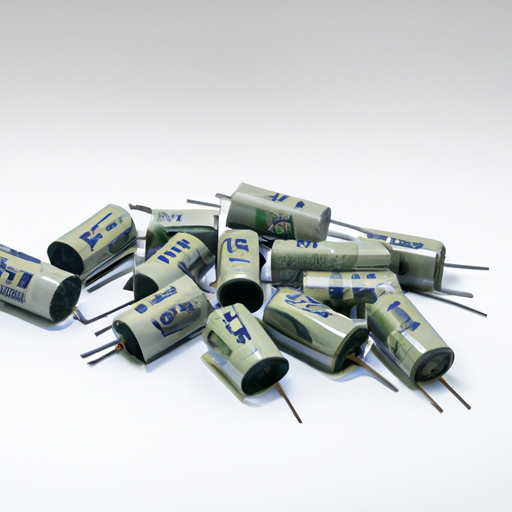
I. Introduction
Film capacitors are essential components in a wide range of electronic devices, from consumer electronics to industrial machinery. These capacitors are known for their reliability, stability, and versatility, making them a popular choice in various applications. However, the effectiveness and safety of film capacitors depend significantly on adherence to established product standards. This article will explore the product standards for film capacitors, their importance, and the challenges manufacturers face in meeting these standards.
II. Understanding Film Capacitors
A. Composition and Structure
Film capacitors consist of a dielectric material sandwiched between two conductive layers. The dielectric materials used can vary, including polyester, polypropylene, and polycarbonate, each offering different electrical properties and performance characteristics. The choice of dielectric material directly influences the capacitor's capacitance, voltage rating, and temperature stability.
1. Dielectric Materials
The dielectric material is crucial in determining the capacitor's performance. For instance, polypropylene film capacitors are known for their low dielectric losses and high insulation resistance, making them suitable for high-frequency applications. In contrast, polyester film capacitors are more cost-effective and widely used in general-purpose applications.
2. Types of Film Capacitors
Film capacitors can be categorized into several types based on their construction and application. Common types include:
Polyester Capacitors: Often used in consumer electronics due to their affordability.
Polypropylene Capacitors: Preferred for high-frequency applications due to their superior performance.
Metalized Film Capacitors: Feature a thin layer of metal deposited on the dielectric, providing self-healing properties.
B. Applications of Film Capacitors
Film capacitors find applications across various sectors, including:
1. Consumer Electronics
In consumer electronics, film capacitors are used in audio equipment, televisions, and power supplies. Their ability to handle high frequencies and provide stable performance makes them ideal for these applications.
2. Industrial Applications
In industrial settings, film capacitors are utilized in motor drives, power converters, and renewable energy systems. Their robustness and reliability are critical in environments where performance is paramount.
3. Automotive and Aerospace
Film capacitors are increasingly used in automotive and aerospace applications, where safety and reliability are non-negotiable. They are employed in power management systems, electronic control units, and safety systems.
III. Importance of Product Standards
A. Ensuring Quality and Reliability
Product standards play a vital role in ensuring the quality and reliability of film capacitors. By adhering to established standards, manufacturers can guarantee that their products meet specific performance criteria, reducing the risk of failure in critical applications.
B. Safety Considerations
Safety is a primary concern in the design and manufacturing of electronic components. Product standards help mitigate risks associated with electrical failures, overheating, and other hazards that could lead to accidents or equipment damage.
C. Regulatory Compliance
Compliance with product standards is often a legal requirement in many regions. Manufacturers must ensure that their products meet local and international regulations to avoid penalties and ensure market access.
D. Market Acceptance and Competitiveness
Products that meet recognized standards are more likely to gain acceptance in the market. Adhering to these standards can enhance a manufacturer's reputation and competitiveness, as customers often prefer products that are certified and reliable.
IV. Key Product Standards for Film Capacitors
A. International Standards
1. IEC (International Electrotechnical Commission)
The IEC sets several standards relevant to film capacitors, including:
IEC 60384 Series: This series outlines the general requirements for fixed capacitors for use in electronic equipment, including film capacitors.
IEC 61071: This standard specifies the requirements for capacitors used in power electronics.
2. ISO (International Organization for Standardization)
ISO 9001: This standard focuses on quality management systems, ensuring that manufacturers maintain consistent quality in their production processes.
B. National Standards
1. ANSI (American National Standards Institute)
ANSI oversees the development of standards in the United States, including those applicable to film capacitors. Compliance with ANSI standards is often required for products sold in the U.S. market.
2. JIS (Japanese Industrial Standards)
JIS standards govern the quality and performance of electronic components in Japan, including film capacitors. Adhering to these standards is crucial for manufacturers targeting the Japanese market.
C. Industry-Specific Standards
1. Automotive Standards (e.g., AEC-Q200)
The AEC-Q200 standard outlines the qualification requirements for passive components used in automotive applications, ensuring that film capacitors can withstand the harsh conditions typical in vehicles.
2. Aerospace Standards (e.g., AS9100)
AS9100 is a widely recognized quality management standard for the aerospace industry. Compliance with this standard is essential for manufacturers supplying components to aerospace applications, including film capacitors.
V. Testing and Certification Processes
A. Types of Tests for Film Capacitors
To ensure compliance with product standards, film capacitors undergo various testing processes, including:
1. Electrical Testing
Electrical tests assess the capacitor's performance characteristics, such as capacitance, voltage rating, and leakage current. These tests ensure that the capacitor operates within specified limits.
2. Environmental Testing
Environmental tests evaluate the capacitor's performance under different conditions, including temperature, humidity, and exposure to chemicals. These tests help determine the capacitor's reliability in real-world applications.
3. Mechanical Testing
Mechanical tests assess the capacitor's durability and resistance to physical stress, such as vibration and shock. These tests are particularly important for applications in automotive and aerospace industries.
B. Certification Bodies
Several organizations provide certification for film capacitors, ensuring compliance with relevant standards:
1. UL (Underwriters Laboratories)
UL is a global safety certification organization that tests and certifies electronic components, including film capacitors, for safety and performance.
2. TUV (Technischer Überwachungsverein)
TUV is a German certification body that provides testing and certification services for various industries, including electronics. Their certification is recognized worldwide.
3. CSA (Canadian Standards Association)
CSA provides certification services for products sold in Canada, ensuring compliance with national safety and performance standards.
VI. Challenges in Meeting Product Standards
A. Technological Advancements
Rapid technological advancements can make it challenging for manufacturers to keep up with evolving standards. As new materials and technologies emerge, standards must be updated to reflect these changes.
B. Material Sourcing and Quality Control
Sourcing high-quality materials is crucial for manufacturing reliable film capacitors. Variability in material quality can lead to inconsistencies in performance, making it difficult to meet standards.
C. Global Supply Chain Issues
Global supply chain disruptions can impact the availability of materials and components needed for manufacturing. These disruptions can hinder a manufacturer's ability to meet production deadlines and maintain compliance with standards.
VII. Future Trends in Film Capacitor Standards
A. Evolving Technologies
As technology continues to evolve, so too will the standards governing film capacitors. Manufacturers must stay informed about emerging technologies and adapt their products accordingly.
B. Sustainability and Environmental Standards
With increasing emphasis on sustainability, future standards may incorporate environmental considerations, such as the use of eco-friendly materials and manufacturing processes.
C. Impact of Digitalization and Smart Technologies
The rise of digitalization and smart technologies will likely influence the development of new standards for film capacitors, particularly in applications related to the Internet of Things (IoT) and smart devices.
VIII. Conclusion
In conclusion, product standards for film capacitors are essential for ensuring quality, safety, and reliability in various applications. These standards not only facilitate regulatory compliance but also enhance market acceptance and competitiveness. As technology evolves, manufacturers must remain vigilant in adapting to new standards and addressing the challenges of material sourcing and global supply chains. By prioritizing compliance and innovation, the film capacitor industry can continue to advance and meet the demands of an ever-changing technological landscape.
IX. References
- IEC 60384 Series: General Requirements for Fixed Capacitors for Use in Electronic Equipment
- ISO 9001: Quality Management Systems
- AEC-Q200: Qualification Requirements for Passive Components
- AS9100: Quality Management Systems for Aerospace
- UL, TUV, and CSA Certification Guidelines
This comprehensive overview of product standards for film capacitors highlights their significance in ensuring the reliability and safety of these critical components in modern electronics. For further information, readers are encouraged to explore the referenced standards and guidelines.