What is the Mainstream Stainless Steel Resistor Production Process?
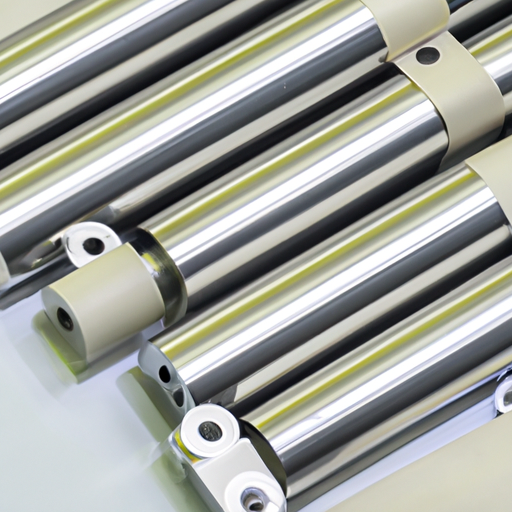
I. Introduction
In the world of electronics, resistors play a crucial role in controlling the flow of electric current. Among the various types of resistors, stainless steel resistors have gained popularity due to their unique properties and advantages. This blog post will explore the mainstream production process of stainless steel resistors, highlighting the significance of each step in ensuring high-quality components for electronic circuits.
II. Understanding Stainless Steel Resistors
A. Composition and Properties of Stainless Steel
Stainless steel is an alloy primarily composed of iron, chromium, and, in some cases, nickel and other elements. The specific composition can vary, leading to different types of stainless steel, such as 304 and 316 grades, which are commonly used in resistor manufacturing. These alloys are known for their excellent corrosion resistance, making them ideal for applications in harsh environments.
1. Types of Stainless Steel Used in Resistors
The choice of stainless steel type is critical in resistor production. For instance, Type 304 stainless steel is often used for its good corrosion resistance and formability, while Type 316 offers enhanced resistance to pitting and crevice corrosion, making it suitable for more demanding applications.
2. Electrical and Thermal Conductivity
While stainless steel is not as conductive as copper or aluminum, it offers a balance of conductivity and resistance, making it suitable for specific resistor applications. Its thermal conductivity also plays a role in heat dissipation, which is essential for maintaining performance under load.
B. Advantages of Stainless Steel Resistors
Stainless steel resistors come with several advantages that make them a preferred choice in various electronic applications.
1. Corrosion Resistance
One of the most significant benefits of stainless steel is its resistance to corrosion. This property ensures that resistors maintain their performance over time, even in challenging environments, such as those exposed to moisture or chemicals.
2. Durability and Longevity
Stainless steel resistors are known for their durability. They can withstand mechanical stress and thermal cycling, which contributes to their longevity. This reliability is crucial in applications where component failure can lead to significant issues.
3. Thermal Stability
The thermal stability of stainless steel resistors allows them to operate effectively across a wide range of temperatures. This characteristic is particularly important in applications where resistors are subjected to varying thermal conditions.
III. The Production Process of Stainless Steel Resistors
The production of stainless steel resistors involves several key steps, each contributing to the final product's quality and performance.
A. Raw Material Selection
1. Sourcing Stainless Steel Alloys
The first step in the production process is sourcing high-quality stainless steel alloys. Manufacturers often work with trusted suppliers to ensure that the materials meet specific standards and specifications.
2. Quality Control Measures for Raw Materials
Quality control is essential at this stage. Incoming materials are subjected to rigorous testing to verify their composition and properties, ensuring that only the best materials are used in production.
B. Design and Engineering
1. Specifications for Resistor Design
Once the raw materials are secured, the design phase begins. Engineers create detailed specifications for the resistors, including dimensions, resistance values, and tolerances.
2. Computer-Aided Design (CAD) Tools in Resistor Development
Modern resistor design often utilizes CAD tools, allowing for precise modeling and simulation of the resistor's performance. This technology helps identify potential issues early in the design process, reducing the likelihood of costly revisions later.
C. Manufacturing Techniques
1. Cutting and Shaping the Stainless Steel
The next step involves cutting and shaping the stainless steel into the desired form. Various methods are employed, including:
Laser Cutting: This technique offers high precision and is ideal for intricate designs.
Stamping: Stamping is a cost-effective method for producing large quantities of resistors with consistent shapes.
Machining: For more complex geometries, machining provides the flexibility needed to achieve precise dimensions.
a. Precision Requirements
Precision is critical in resistor manufacturing, as even minor deviations can affect the resistor's performance. Manufacturers invest in advanced machinery and skilled operators to ensure high-quality production.
2. Resistance Element Fabrication
The resistance element is the heart of the resistor. Various techniques are used to create these elements, including:
Thin Film Technology: This method involves depositing a thin layer of resistive material onto a substrate, allowing for precise control over resistance values.
Thick Film Technology: In this approach, a paste containing resistive materials is printed onto a substrate and then fired to create the resistive element.
a. Importance of Resistance Value Accuracy
Achieving accurate resistance values is crucial for the performance of electronic circuits. Manufacturers employ strict quality control measures to ensure that each resistor meets its specified resistance value.
D. Assembly Process
1. Combining Resistive Elements with Terminals
Once the resistive elements are fabricated, they are combined with terminals to create the final resistor. This step requires careful handling to avoid damaging the delicate components.
2. Soldering and Welding Techniques
Soldering and welding are commonly used to secure the resistive elements to the terminals. These techniques must be performed with precision to ensure strong connections that can withstand thermal and mechanical stress.
3. Quality Assurance During Assembly
Quality assurance is a continuous process throughout assembly. Manufacturers conduct inspections and tests to verify that each resistor meets the required specifications before moving on to the next stage.
E. Coating and Finishing
1. Application of Protective Coatings
To enhance the durability and performance of stainless steel resistors, protective coatings are often applied. These coatings can provide additional corrosion resistance and improve the resistor's overall lifespan.
2. Surface Treatments for Enhanced Performance
Surface treatments, such as passivation, can further improve the corrosion resistance of stainless steel resistors. This process removes free iron and enhances the formation of a protective oxide layer.
3. Importance of Aesthetics and Branding
In addition to performance, aesthetics play a role in resistor production. Manufacturers often consider branding and visual appeal, ensuring that the final product is not only functional but also attractive.
IV. Testing and Quality Control
A. Electrical Testing Methods
1. Resistance Measurement
Electrical testing is a critical step in the production process. Resistance measurements are taken to ensure that each resistor meets its specified value.
2. Temperature Coefficient Testing
Temperature coefficient testing evaluates how the resistance value changes with temperature. This information is essential for applications where resistors will experience varying thermal conditions.
B. Mechanical Testing
1. Stress and Strain Analysis
Mechanical testing assesses the physical properties of the resistors, including their ability to withstand stress and strain. This testing helps identify potential weaknesses in the design or materials.
2. Durability Assessments
Durability assessments simulate real-world conditions to evaluate how resistors perform over time. This testing is crucial for ensuring long-term reliability.
C. Compliance with Industry Standards
1. ISO Certifications
Manufacturers often seek ISO certifications to demonstrate their commitment to quality and consistency in production processes.
2. RoHS and REACH Compliance
Compliance with environmental regulations, such as RoHS (Restriction of Hazardous Substances) and REACH (Registration, Evaluation, Authorisation, and Restriction of Chemicals), is essential for manufacturers to ensure that their products are safe and environmentally friendly.
V. Packaging and Distribution
A. Packaging Materials and Methods
Once the resistors pass all quality control tests, they are packaged for distribution. Packaging materials must protect the resistors from damage during transport while also being environmentally friendly.
B. Logistics and Supply Chain Considerations
Efficient logistics and supply chain management are crucial for timely delivery to customers. Manufacturers must coordinate with suppliers and distributors to ensure that products reach their destinations without delays.
C. Importance of Proper Labeling and Documentation
Proper labeling and documentation are essential for traceability and compliance with industry standards. Each package should include information about the resistor's specifications, testing results, and compliance certifications.
VI. Innovations and Future Trends
A. Advances in Materials Science
Ongoing research in materials science is leading to the development of new stainless steel alloys with improved properties, enhancing the performance of resistors.
B. Automation and Smart Manufacturing
The integration of automation and smart manufacturing technologies is streamlining the production process, increasing efficiency, and reducing costs.
C. Environmental Considerations in Production
As sustainability becomes a priority, manufacturers are exploring eco-friendly production methods and materials to minimize their environmental impact.
VII. Conclusion
The production process of stainless steel resistors is a complex and meticulous endeavor that involves multiple stages, from raw material selection to final testing and distribution. Each step is crucial in ensuring that the resistors meet the high standards required for modern electronic applications. As technology continues to advance, the future of stainless steel resistors looks promising, with innovations in materials and manufacturing processes paving the way for even better performance and sustainability.
VIII. References
- Academic journals and articles on materials science and resistor technology.
- Industry reports detailing trends and standards in resistor manufacturing.
- Manufacturer guidelines and specifications for stainless steel resistors.
This comprehensive overview of the mainstream stainless steel resistor production process highlights the intricate steps involved in creating reliable and durable components essential for electronic circuits.
What is the Mainstream Stainless Steel Resistor Production Process?
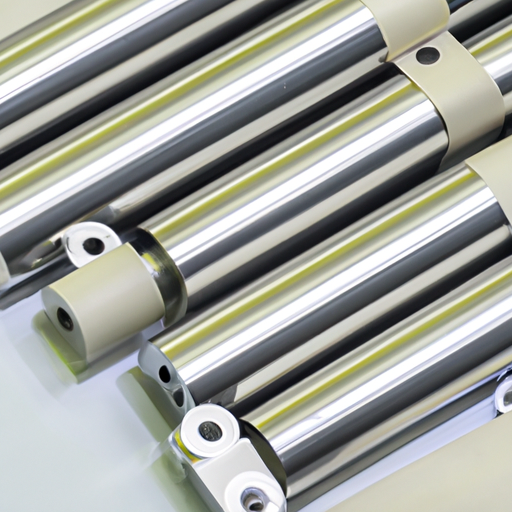
I. Introduction
In the world of electronics, resistors play a crucial role in controlling the flow of electric current. Among the various types of resistors, stainless steel resistors have gained popularity due to their unique properties and advantages. This blog post will explore the mainstream production process of stainless steel resistors, highlighting the significance of each step in ensuring high-quality components for electronic circuits.
II. Understanding Stainless Steel Resistors
A. Composition and Properties of Stainless Steel
Stainless steel is an alloy primarily composed of iron, chromium, and, in some cases, nickel and other elements. The specific composition can vary, leading to different types of stainless steel, such as 304 and 316 grades, which are commonly used in resistor manufacturing. These alloys are known for their excellent corrosion resistance, making them ideal for applications in harsh environments.
1. Types of Stainless Steel Used in Resistors
The choice of stainless steel type is critical in resistor production. For instance, Type 304 stainless steel is often used for its good corrosion resistance and formability, while Type 316 offers enhanced resistance to pitting and crevice corrosion, making it suitable for more demanding applications.
2. Electrical and Thermal Conductivity
While stainless steel is not as conductive as copper or aluminum, it offers a balance of conductivity and resistance, making it suitable for specific resistor applications. Its thermal conductivity also plays a role in heat dissipation, which is essential for maintaining performance under load.
B. Advantages of Stainless Steel Resistors
Stainless steel resistors come with several advantages that make them a preferred choice in various electronic applications.
1. Corrosion Resistance
One of the most significant benefits of stainless steel is its resistance to corrosion. This property ensures that resistors maintain their performance over time, even in challenging environments, such as those exposed to moisture or chemicals.
2. Durability and Longevity
Stainless steel resistors are known for their durability. They can withstand mechanical stress and thermal cycling, which contributes to their longevity. This reliability is crucial in applications where component failure can lead to significant issues.
3. Thermal Stability
The thermal stability of stainless steel resistors allows them to operate effectively across a wide range of temperatures. This characteristic is particularly important in applications where resistors are subjected to varying thermal conditions.
III. The Production Process of Stainless Steel Resistors
The production of stainless steel resistors involves several key steps, each contributing to the final product's quality and performance.
A. Raw Material Selection
1. Sourcing Stainless Steel Alloys
The first step in the production process is sourcing high-quality stainless steel alloys. Manufacturers often work with trusted suppliers to ensure that the materials meet specific standards and specifications.
2. Quality Control Measures for Raw Materials
Quality control is essential at this stage. Incoming materials are subjected to rigorous testing to verify their composition and properties, ensuring that only the best materials are used in production.
B. Design and Engineering
1. Specifications for Resistor Design
Once the raw materials are secured, the design phase begins. Engineers create detailed specifications for the resistors, including dimensions, resistance values, and tolerances.
2. Computer-Aided Design (CAD) Tools in Resistor Development
Modern resistor design often utilizes CAD tools, allowing for precise modeling and simulation of the resistor's performance. This technology helps identify potential issues early in the design process, reducing the likelihood of costly revisions later.
C. Manufacturing Techniques
1. Cutting and Shaping the Stainless Steel
The next step involves cutting and shaping the stainless steel into the desired form. Various methods are employed, including:
Laser Cutting: This technique offers high precision and is ideal for intricate designs.
Stamping: Stamping is a cost-effective method for producing large quantities of resistors with consistent shapes.
Machining: For more complex geometries, machining provides the flexibility needed to achieve precise dimensions.
a. Precision Requirements
Precision is critical in resistor manufacturing, as even minor deviations can affect the resistor's performance. Manufacturers invest in advanced machinery and skilled operators to ensure high-quality production.
2. Resistance Element Fabrication
The resistance element is the heart of the resistor. Various techniques are used to create these elements, including:
Thin Film Technology: This method involves depositing a thin layer of resistive material onto a substrate, allowing for precise control over resistance values.
Thick Film Technology: In this approach, a paste containing resistive materials is printed onto a substrate and then fired to create the resistive element.
a. Importance of Resistance Value Accuracy
Achieving accurate resistance values is crucial for the performance of electronic circuits. Manufacturers employ strict quality control measures to ensure that each resistor meets its specified resistance value.
D. Assembly Process
1. Combining Resistive Elements with Terminals
Once the resistive elements are fabricated, they are combined with terminals to create the final resistor. This step requires careful handling to avoid damaging the delicate components.
2. Soldering and Welding Techniques
Soldering and welding are commonly used to secure the resistive elements to the terminals. These techniques must be performed with precision to ensure strong connections that can withstand thermal and mechanical stress.
3. Quality Assurance During Assembly
Quality assurance is a continuous process throughout assembly. Manufacturers conduct inspections and tests to verify that each resistor meets the required specifications before moving on to the next stage.
E. Coating and Finishing
1. Application of Protective Coatings
To enhance the durability and performance of stainless steel resistors, protective coatings are often applied. These coatings can provide additional corrosion resistance and improve the resistor's overall lifespan.
2. Surface Treatments for Enhanced Performance
Surface treatments, such as passivation, can further improve the corrosion resistance of stainless steel resistors. This process removes free iron and enhances the formation of a protective oxide layer.
3. Importance of Aesthetics and Branding
In addition to performance, aesthetics play a role in resistor production. Manufacturers often consider branding and visual appeal, ensuring that the final product is not only functional but also attractive.
IV. Testing and Quality Control
A. Electrical Testing Methods
1. Resistance Measurement
Electrical testing is a critical step in the production process. Resistance measurements are taken to ensure that each resistor meets its specified value.
2. Temperature Coefficient Testing
Temperature coefficient testing evaluates how the resistance value changes with temperature. This information is essential for applications where resistors will experience varying thermal conditions.
B. Mechanical Testing
1. Stress and Strain Analysis
Mechanical testing assesses the physical properties of the resistors, including their ability to withstand stress and strain. This testing helps identify potential weaknesses in the design or materials.
2. Durability Assessments
Durability assessments simulate real-world conditions to evaluate how resistors perform over time. This testing is crucial for ensuring long-term reliability.
C. Compliance with Industry Standards
1. ISO Certifications
Manufacturers often seek ISO certifications to demonstrate their commitment to quality and consistency in production processes.
2. RoHS and REACH Compliance
Compliance with environmental regulations, such as RoHS (Restriction of Hazardous Substances) and REACH (Registration, Evaluation, Authorisation, and Restriction of Chemicals), is essential for manufacturers to ensure that their products are safe and environmentally friendly.
V. Packaging and Distribution
A. Packaging Materials and Methods
Once the resistors pass all quality control tests, they are packaged for distribution. Packaging materials must protect the resistors from damage during transport while also being environmentally friendly.
B. Logistics and Supply Chain Considerations
Efficient logistics and supply chain management are crucial for timely delivery to customers. Manufacturers must coordinate with suppliers and distributors to ensure that products reach their destinations without delays.
C. Importance of Proper Labeling and Documentation
Proper labeling and documentation are essential for traceability and compliance with industry standards. Each package should include information about the resistor's specifications, testing results, and compliance certifications.
VI. Innovations and Future Trends
A. Advances in Materials Science
Ongoing research in materials science is leading to the development of new stainless steel alloys with improved properties, enhancing the performance of resistors.
B. Automation and Smart Manufacturing
The integration of automation and smart manufacturing technologies is streamlining the production process, increasing efficiency, and reducing costs.
C. Environmental Considerations in Production
As sustainability becomes a priority, manufacturers are exploring eco-friendly production methods and materials to minimize their environmental impact.
VII. Conclusion
The production process of stainless steel resistors is a complex and meticulous endeavor that involves multiple stages, from raw material selection to final testing and distribution. Each step is crucial in ensuring that the resistors meet the high standards required for modern electronic applications. As technology continues to advance, the future of stainless steel resistors looks promising, with innovations in materials and manufacturing processes paving the way for even better performance and sustainability.
VIII. References
- Academic journals and articles on materials science and resistor technology.
- Industry reports detailing trends and standards in resistor manufacturing.
- Manufacturer guidelines and specifications for stainless steel resistors.
This comprehensive overview of the mainstream stainless steel resistor production process highlights the intricate steps involved in creating reliable and durable components essential for electronic circuits.